Robotic welding systems are made up of several important components, all of which work together to create a high-quality weld. The first component is the robotic arm, which is responsible for moving the welding torch or electrode in order to create the desired weld pattern. Next is the power source, which provides the necessary electricity to heat up the metal and create the weld.
Finally, there is the welding torch or electrode itself, which actually does the work of melting the metal and joining it together.
Robotic welding is a process that uses robotic arms to weld metal components together. This process is often used in the automotive industry, as it is efficient and can produce high-quality welds. There are several components that make up a robotic welding system, which include:
-The controller, which controls the movement of the robotic arm and manages the welding process
-The power source, which provides power to the controller and other parts of the system
-The torch, which conducts heat to melt the metal and create the weld
-The wire feeder, which supplies filler material to create a strong joint between two pieces of metal
Robotic Welding Pdf
Robotic welding is a type of arc welding that uses robots to carry out the weld. The robot is programmed to follow a path that has been set by the operator, and the welding torch is mounted on the robot arm. Robotic welding can be used for a variety of metals, including aluminum, stainless steel, and mild steel.
There are many benefits to using robotic welding over traditional methods. For example, robotic welds are more precise and have less potential for error. In addition, robotic welding can be carried out in difficult-to-reach places or in situations where it would be difficult for a human welder to operate safely.
Finally, robotic welders can work faster than human welders, which increases productivity.
If you’re considering implementing robotic welding into your business, there are a few things you should keep in mind. First, you’ll need to invest in quality equipment – this is not an area where you want to cut corners.
Second, you’ll need to train your operators how to use the new technology. And third, you’ll need to have realistic expectations about what robotic welding can do for your business – it’s not a magic solution that will solve all of your problems overnight!
Robotic Welding, Programming Pdf
Robotic welding is a process where an operator uses a computer to control the movements of a welding robot. The operator can program the robot to weld in a specific pattern and direction, which allows for consistent and accurate welds. This type of welding is often used in industries where there is a high demand for precision welds, such as the automotive industry.
There are many benefits to using robotic welding over traditional methods. For one, it can greatly increase productivity as the robots can work faster and more accurately than human operators. Additionally, it can help improve safety as there is no need for operators to be in close proximity to the welding area.
Robotic welding also offers greater flexibility as the robots can be programmed to weld different materials and thicknesses.
If you’re considering implementing robotic welding in your business, there are a few things you should keep in mind. First, you will need to have someone on staff who is able to program the robots.
Second, you’ll need to have a dedicated area for the robots to operate in that is free of debris and other hazards. Finally, you’ll need to make sure that your workers are properly trained on how to use the system safely before starting production.
Robotic Welding Systems
Robotic welding is a process where an operator controls a welding machine using a computer. This type of welding is used in various industries, such as the automotive and aerospace industries, where it is difficult to weld manually. Robotic welding systems are classified into three types: spot, seam, and projection welding.
Spot Welding
Spot welding is the most commonly used type of robotic welding. In this process, two pieces of metal are clamped together and an electrode is placed on each side of the joint.
An electric current is then passed through the electrodes, which heat up and weld the two pieces of metal together. Spot welds are typically used for joining thin sheets of metal together.
Seam welding is similar to spot welding, but instead of using two electrodes, only one electrode is used. The electrode moves along the length of the joint as it welds the two pieces of metal together. Seam welds are typically used for joining thicker sheets of metal together.
Projection Welding Projection welding is a type of spot welding that uses projections on one or both sides of the joint to focus the electric current onto a small area. This allows for a stronger weld to be achieved without having to heat up the entire area around the joint.
Projection welds are typically used for joining thick sheets of metal together.
Use of Robots in Welding
Robots have been used in welding for many years now and their use has increased steadily over time. There are several reasons for this, the main ones being that robots are much more precise than humans, they never get tired and can work for longer hours, and they don’t require any breaks. This means that companies can save a lot of money by using robots for their welding needs.
There are different types of welding robots available on the market, each with its own advantages and disadvantages. The most common type is the arc welding robot, which is often used for tasks such as spot welding and seam welding. These robots are very precise and can weld two pieces of metal together perfectly every time.
However, they can be quite expensive to purchase and maintain.
Another type of welding robot is the resistance welding robot, which is often used for tasks such as butt welding and lap joint Welding . These robots are not as precise as arc welding robots but they are much cheaper to buy and maintain.
Resistance welding robots also have the advantage of being able to weld two pieces of metal together very quickly.
The final type of welding robot is the plasma cutting robot, which is often used for tasks such as cutting holes in metal sheets or pipes. Plasma cutting robots are very fast and can cut through metal very quickly but they can be quite dangerous to use if you’re not careful.
Whichever type of robotics technology you decide to use for your business’ needs, there’s no doubt that it will save you money in the long run by increasing productivity levels and reducing mistakes made by human workers .
Robotic Welding in Automotive Industry
Robots have been increasingly used in automotive welding in recent years. There are several reasons for this trend:
1. Robots are more precise than humans, so they can produce higher-quality welds.
2. Robots can work faster than humans, so they can increase production rates.
3. Robots can work continuously without getting tired, so they can reduce overall costs.
4. Robots don’t require breaks and can work in difficult or dangerous environments that would be unsuitable for humans.
5. Automotive companies are under pressure to reduce emissions and improve fuel economy, so they are turning to robots to help them meet these goals.
Robotic Welding History
Robotic welding is a process that uses mechanized arms to weld metal parts together. This technology has been around since the early 1960s, but it was not widely used in manufacturing until the 1980s.Since then, robotic welding has become increasingly popular, particularly in the automotive industry where it is used to weld together car body parts.
The main advantage of robotic welding over traditional welding methods is that it is much more precise and can be done faster.
This results in a stronger bond between the metal parts and less chance of defects. Additionally, robotic welding is less likely to cause health problems for workers since they are not exposed to fumes and heat like they would be with other welding methods.
There are two types of robotic welding: arc welding and resistance spot welding.
Arc welding uses an electric arc to melt the metals together, while resistance spot Welding uses pressure and heat to fuse the metals together. Both methods have their advantages and disadvantages, so it’s important to choose the right one for your project.
Introduction to Robotic Welding
Robotic welding is a type of welding that uses robots to weld metal parts together. This process is known for being faster and more precise than traditional welding methods. It can be used to weld various metals, including aluminum, stainless steel, and mild steel.
There are several advantages to using robotic welding. First, it is much faster than traditional methods. This means that production times can be shorter and more parts can be produced in a given time period.
Second, robotic welding is more precise than manual welding, which results in less waste and fewer defects. Finally, because robots do not get tired, they can work for longer periods of time without breaks, which increases productivity even further.
Despite these advantages, there are some disadvantages to robotic welding as well.
One is the initial cost of investing in the necessary equipment. Another potential downside is that if something goes wrong with the robot during operation, it can be difficult to fix or replace quickly. Additionally, because robotic welders are controlled by computers, they require operators with the skillset needed to program them correctly.
Robotic Mig Welding Speed
Robotic mig welding speed is determined by a number of factors, including the type of wire being used, the thickness of the material being welded, and the amperage and voltage settings on the welder. Wire diameter, welding speed and torch travel speed are also important variables to consider when setting up a robotic mig welder.
The most common Mig wire used in robotic welding applications is .035″ (0.9mm) diameter mild steel wire. This wire size will work well for most materials up to 3/16″ (4.8mm) thick.
When welding thicker materials, you may need to use a larger diameter wire such as .045″ (1.2mm).
Wire feed speed is measured in inches per minute (ipm) or meters per minute (mpm). The recommended range for .035″ (0.9mm) mild steel wire is 280-420 ipm (.45-.7 m/s).
Amperage and voltage settings will vary depending on the application and material being welded but can be set using an online calculator or by following the manufacturer’s recommendations.
Travel speed is another important factor to consider when setting up your robotic mig welder. Travel speed too slow can result in excessive heat input and distortion while too fast can cause lack of fusion or incomplete penetration.
A good rule of thumb is to start with a travel speed that is half of your wirespeed in ipm (.45 x wirespeed m/s). For example, if you are using .035″ (0.9mm) mild steel wire at 400 ipm (.6 m/s), you would want to start with a travel speed around 200 ipm (.3 m/s).
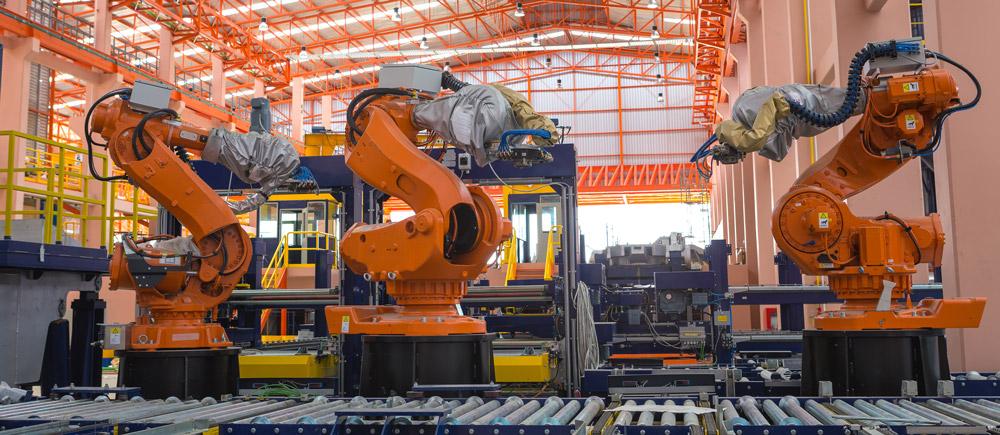
Credit: www.thefabricator.com
What is Robotic Welding System?
Robotic welding is a type of arc welding process that uses a robotic arm to weld metal components together. The robotic arm is controlled by a computer program that determines the welding parameters, such as electrode size, electrode position and welding speed. Robotic welding systems are used in many industries, including automotive manufacturing, aerospace engineering and shipbuilding.
There are several advantages to using robotic welding over traditional manual or semiautomatic welding processes. First, robotic welders can work faster than human welders, which increases productivity and decreases costs. Second, robotic welders can create consistent welds with little variation from one part to the next.
This repeatability is important in industries where product quality is essential, such as the automotive industry. Third, robotic welders can access hard-to-reach areas of a workpiece that would be difficult for human welders to reach. This allows for more complete coverage of the joint area and results in stronger welds.
Disadvantages of robotic welding include the high initial cost of the equipment and the need for skilled operators who understand how to program and maintain the robots. In addition, because they are automated machines, there is always the potential for malfunction or failure which could lead to production delays or scrap parts.
What are the Types of Robots in Welding?
Welding robots are classified according to their degree of freedom, which is the number of independent axes of motion they possess. The three main types of welding robots are point-to-point, linear, and articulated.
Point-to-point welding robots have the simplest construction and the fewest degrees of freedom.As their name implies, they move in a straight line between two points, making them well suited for applications where accuracy and repeatability are not critical. Linear welding robots have more degrees of freedom than point-to-point models and can move along multiple axes simultaneously. This allows them to weld complex shapes that would be difficult or impossible for a point-to-point robot to handle.
Articulated welding robots have the most degrees of freedom of any type and can rotate about multiple joints. This gives them great flexibility and makes them ideal for welding objects with irregular surfaces or in tight spaces.
What Features are Required for Robot in Spot Welding?
Spot welding is a process in which two pieces of metal are joined together by heating them with an electric arc. This process is commonly used in the manufacturing of cars and other objects made from sheet metal. In order for spot welding to be successful, there are certain features that are required for the robot that performs this task.
The most important feature of a spot welding robot is its ability to generate heat. This heat is necessary in order to melt the metal so that it can be joined together. The robot must also have a way to apply pressure to the two pieces of metal so that they remain in contact with each other while they are being heated.
Another important feature of a spot welding robot is its ability to move around. This is necessary because the spot welding process usually requires multiple welds in order to join two pieces of metal together securely. The robot must be able to move its arm so that it can reach all of the areas where welds need to be made.
The last major feature that is required for a spot welding robot is safety precautions. This type of welding produces a lot of heat and sparks, which can pose a danger to workers who are nearby. The robot must have some type of enclosure or barrier around it so that workers cannot come into contact with the hot metals or sparks.
What is Robotic Welding Called?
In industrial welding, robotic welding is a sub-type of automated welding in which operator control over the welder is passed to a computer program. The program then determines the best weld parameters for the given workpiece geometry and material type. This process generally results in increased productivity and consistency compared to manual welding.
The term “robotic welding” can be misleading, as it implies that the entire process is automated. In reality, robotic welding systems still require an operator to load and unload parts, as well as set up the initial parameters for each weld joint. However, once these tasks are completed, the robot takes over and handles all aspects of the welding process itself.
One advantage of robotic welding is that it allows for much more consistent welds than can be achieved by human operators. This is due to both the repeatability of robot motion and the ability of computer programs to precisely control weld variables such as voltage, amperage, and gas flow rates. As a result, robotic welds are often stronger and more aesthetically pleasing than those done by hand.
Another benefit of robotic welding is increased productivity. Since robots do not need to take breaks and can work around the clock if necessary, they can significantly increase output in a given time period compared to human workers. Additionally, multiple robots can often be used on one production line, further increasing throughput capacity.
Robotic Welding Basics-E.P-01 , F.T-OTC Daihen Robot.
Conclusion
Robotic welding systems typically consist of three main components: the robot arm, the power source, and the weld torch. The robotic arm is a computer-controlled device that moves the weld torch in pre-programmed patterns to create the desired welds. The power source provides electricity to heat the welding torch and melt the metal being joined.
The weld torch melts the metal and joins it together as it cools.