H13 tool steel is a chromium-molybdenum-vanadium alloy that is known for its toughness and resistance to abrasion and impact. Welding H13 can be a challenge because of its high carbon content and hardening properties, but it can be done with the right equipment and techniques. Here are some tips on how to weld H13 tool steel.
- H13 tool steel is an air-hardening, hot work 5% chromium die steel
- It is an excellent choice for a wide range of hot work and cold work applications
- An H13 tool steel bar is heated to 950°C (1742°F) and then cooled in oil or water
- This gives the metal greater hardness and toughness than if it were quenched in air alone
- The steel is then reheated to 1150°C (2102°F), which is above the critical temperature for austenite, and held at this temperature for 30 minutes per 25 mm of thickness (1 hour per inch)
- Finally, it is cooled gradually in air back down to room temperature over a period of 2–3 hours or more, depending on the size of the piece being welded
Tig Welds
If you’re looking for information on Tig Welds, you’ve come to the right place. In this blog post, we’ll cover everything you need to know about Tig Welds, including what they are, how they work, and what advantages they offer over other welding methods.
So, what is a Tig Weld?
A Tig Weld is a type of arc welding that uses an tungsten electrode to produce the weld. The tungsten electrode is non-consumable, which means it doesn’t melt during the welding process. This makes Tig Welds ideal for welding thin materials or for projects where precision is key.
How does a Tig Weld work? During a Tig Weld, an electric current passes through the tungsten electrode and creates an arc. The heat from the arc melts the metal being welded, which fuse together as they cool.
What are the advantages of using a Tig Weld? There are many advantages to using a Tig Weld over other welding methods. One advantage is that it produces cleaner welds with less contamination than other methods.
Additionally, because the tungsten electrode doesn’t melt during welding, it’s possible to weld thinner materials without fear of burning through them. And finally, since there’s no melting involved in a Tig Weld, there’s less distortion and warping of the material being welded – making it ideal for projects where precision is key.
Tig Vs Mig Welding
When it comes to welding, there are a few different options to choose from. Two of the most popular welding methods are Tig and Mig welding. So, what’s the difference between the two?
Tig Welding
Tig (tungsten inert gas) welding is a type of arc welding that uses a non-consumable tungsten electrode to create an arc between the metal being welded and the welder. The welder then uses filler metal to add material to the joint.
Tig welding is often used for thin metals, as it provides a very clean and precise weld. It can be used on aluminum, magnesium, stainless steel, and other metals.
Mig Welding
Mig (metal inert gas) welding is another type of arc welding that uses an electrode that is fed through a wire feeder machine. The electrode melts as it comes into contact with the metal being welded, forming a pool of molten metal. The welder then adds filler metal to this pool in order to create a strong joint.
Mig welding is faster than Tig welding and can be used on thicker metals.
What is Tig Welding
Tig welding is a popular welding process that uses an arc to weld metals together. The Tig process is similar to MIG welding, but instead of using a wire feeder, the welder uses a tungsten electrode to create the arc. This process can be used on a variety of metals, including aluminum, stainless steel, and even titanium.
Tig welding is often used in applications where aesthetics are important, as it produces a clean weld with minimal spatter.
Gtaw Welding
Gas tungsten arc welding (GTAW), also known as tungsten inert gas (TIG) welding, is an arc welding process that uses a non-consumable tungsten electrode to produce the weld. The weld area and electrode are protected from oxidation or other atmospheric contamination by an inert shielding gas (argon or helium). A filler metal may or may not be used, though almost always used with aluminum and magnesium alloys.
GTAW is most commonly used to weld thin sections of stainless steel and non-ferrous metals such as aluminum, magnesium, and copper alloys. The process grants the operator greater control over the weld than competing processes such as shielded metal arc welding and gas metal arc welding, allowing for stronger, higher quality welds. However, GTAW is comparatively more complex and difficult to master, making it sometimes unsuitable for rapid prototyping and mass production.
A major advantage of GTAW over earlier welding processes is its ability to produce very clean, precise welds without producing any smoke or fumes. This is due to the fact that there is no consumable electrode in GTAW; instead, an electric arc between the workpiece and a non-consumable tungsten electrode produces heat which melts both the base metal and any filler material being used. The lack of a consumable electrode also means that there is no need to continually stop welding in order to replace it – a significant time saving compared to other processes.
In addition, GTAW can be performed in nearly any position – even upside down! – thanks to the torch’s ability to be rotated in nearly 360 degrees around the workpiece.
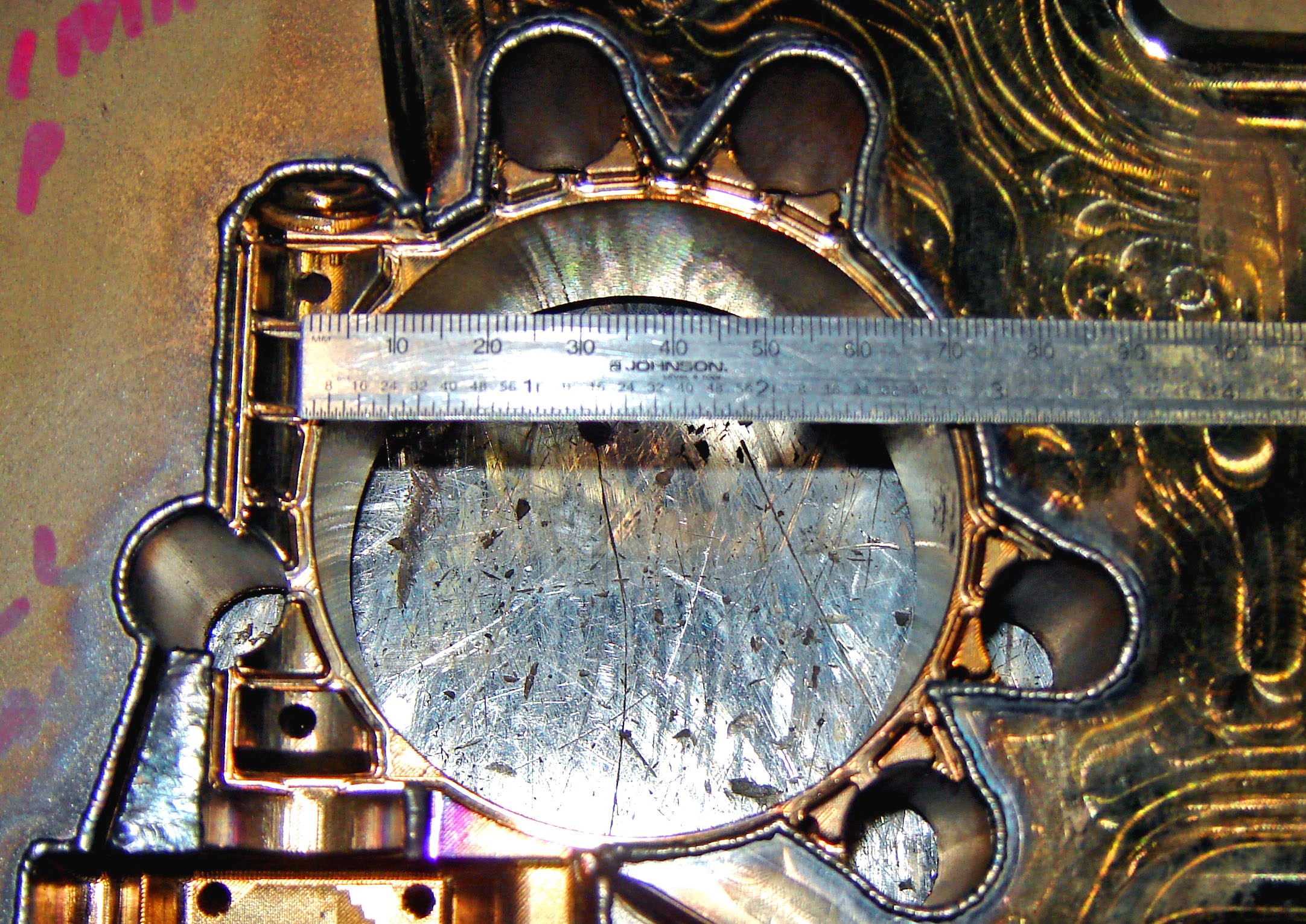
Credit: www.mpdweldinginc.com
Can You Weld H13 Steel?
H13 is an extremely versatile hot work tool steel that has a high resistance to cracking, good thermal conductivity, and a deep hardenability. It can be used for a wide variety of applications such as die casting dies, extrusion tools, hot forging dies, hot gripper dies, and plastic injection molds. H13 can also be used for high temperature applications such as in Furnace Rollers and Refractory Anchors.
Can Tool Steel Be Welded?
Tool steel is a type of steel that is known for its hardness and resistance to wear. Because of these properties, tool steel is often used in applications where tools or parts are subject to high levels of wear, such as in cutting and drilling operations. Tool steel can be welded, but it is important to use the correct welding procedures and techniques.
Using the wrong welding methods can result in tool steel that is brittle and difficult to work with.
Can You Forge Weld H13?
Yes, H13 can be forge welded. In order to do so, the metal must first be heated until it is malleable enough to be forged. Once it has reached the appropriate temperature, two pieces of H13 can be placed together and welded using a forge welding process.
This type of welding results in a strong bond between the two pieces of metal.
How Do You Weld Hardened Steel?
If you’re looking to weld hardened steel, there are a few things you need to know. Hardened steel is difficult to weld because it has been heat treated to be harder and more durable. This means that the metal has been through a process of heating and cooling that makes it more resistant to wear and tear.
However, this also makes the metal more difficult to work with. When welding hardened steel, you need to use a higher temperature than you would for regular steel. This will help the metals melt together better so that you can create a strong bond.
You also need to be extra careful not to overheat the metal, as this can cause warping or other damage. If possible, it’s best to practice on some scrap pieces beforeAttemptingto weld your project piece. With the right preparation and care, welding hardened steel is definitely possible!
TIG Welding with TOOL STEEL filler?!
Conclusion
If you’re looking to weld H13 tool steel, there are a few things you need to know. First, H13 tool steel is highly alloyed and contains chromium, molybdenum, and vanadium. This makes it ideal for applications that require high wear resistance and toughness.
Second, H13 tool steel can be difficult to weld due to its high hardness. But with the right techniques and tools, it’s definitely doable.
Here’s a step-by-step guide on how to weld H13 tool steel:
1. Preheat the material before welding. This will help prevent cracking during cooling.
2. Use a low hydrogen electrode when welding.
This will also help prevent cracks during cooling.
3. Keep your welds short and sweet. Longer welds increase the likelihood of cracking during cooling.
4. Cool the material slowly after welding is complete. Rapid cooling can cause cracking as well.