If you are looking for an electric welding system, it is important to consider the cost of operating the system. There are a few things that will affect the electric cost of a welding system, and it is important to be aware of these factors before making a purchase. The size of the unit, whether it is single or three phase, and the number of hours you plan on using the unit each day all play a role in how much your monthly electric bill will be.
- Look at the wattage of the welding system
- Convert the wattage to kilowatts
- Find the cost per kilowatt hour from your electric company
- Multiply the cost per kilowatt hour by the number of kilowatts used by the welding system
Welding Cost Calculator
If you are in the market for a welder, you may be wondering about the cost of welding. There are many variables to consider when it comes to welding costs, including the type of welders, materials, and labor. If you want to get an accurate estimate of welding costs, it is important to use a welding cost calculator.
There are many different types of welders on the market today. The two most common types are MIG and TIG welders. MIG welders use a wire that is fed through a gun and melted by an electric arc.
TIG welders use a tungsten electrode that is also melted by an electric arc. Both types of welders can be used for metal fabrication projects.
The cost of materials will vary depending on the type of metal being used.
Aluminum is one of the most expensive metals to weld, while steel is one of the least expensive metals. The thickness of the metal will also affect the cost as thicker metals require more time and effort to weld than thinner metals.
Labor costs will also play a role in overall welding costs.
If you plan on doing the welding yourself, then your labor costs will be minimal. However, if you hire someone else to do the welding for you, their hourly rate will need to be factored into your overall costs.
A welding cost calculator can help you determine all of these factors so that you can get an accurate estimate for your project.
By inputting all relevant information into the calculator, you can get a detailed report that includes estimated material and labor costs as well as other important details such as project duration and equipment needed.
200 Amp Welding Machine Power Consumption
Welding machines are a vital part of any metalworking shop. They come in a variety of sizes and power levels, but the most important factor to consider when choosing a welding machine is its amperage rating. This number indicates the maximum amount of current that the machine can output, and it plays a big role in determining the types of materials that can be welded as well as the thicknesses of those materials.
In general, higher-amp welding machines are capable of welding thicker materials than lower-amp machines. But there’s more to consider than just amperage when it comes to welding machine power consumption. For example, some machines may have a higher duty cycle, which means they can run for longer periods of time without overloading or overheating.
When it comes to choosing a welding machine, it’s important to consult with an expert to determine the best option for your needs. But knowing the basics about amp ratings and power consumption will help you narrow down your options and make an informed decision about which machine is right for you.
Welding Machine Input Current Calculation
Welding machine input current calculation is very important for any welder. It is a simple mathematical equation that allows the welder to determine the correct welding current necessary to produce a sound weld. The formula takes into account the welding machine’s rated output amperage and the electrode’s diameter.
By using this information, the welder can calculate the amount of welding current required to produce a quality weld.
250 Amp Welding Machine Wattage
If you’re in the market for a welding machine that can handle big jobs, you’ll want to consider a 250 amp welding machine. These machines are powerful and can weld thick materials quickly and easily. But before you purchase one, it’s important to understand the wattage requirements of these machines.
Most 250 amp welding machines require at least 30 amps of power to operate. That means you’ll need a dedicated circuit that can provide that much power. If you try to use a lower amp circuit, the welding machine will likely trip the breaker or overheat.
And if you’re using an extension cord, make sure it’s rated for at least 30 amps as well.
In terms of watts, most 250 amp welding machines require around 7500 watts of power. So if you’re using a generator, make sure it can provide enough power for the welding machine.
The last thing you want is to be in the middle of a job and have your welding machine shut down because there’s not enough power!
3 Phase Welding Machine Power Connection
If you’re a welder, chances are you’ve used a 3 phase welding machine. But do you know how to properly connect the power to your machine? If not, don’t worry – we’re here to help!
The first thing you’ll need to do is determine which type of power supply you have. There are three types of 3 phase power: wye (Y), delta (Δ), and ungrounded delta. Once you know which type of power supply you have, follow the steps below to make sure your machine is properly connected.
Wye Power Supply:
1. Connect the black lead from your machine to one of the black leads on the power supply.
2. Connect the red lead from your machine to one of the red leads on the power supply.
3. Connect the blue lead from your machine to one of the blue leads on the power supply.
4. Make sure all connections are tight and secure before starting your weld!
Delta Power Supply:
1)Connect only two wires fromthe welding machineto any two phasesof aconnection boxor receptacle that hasthree phaseterminals.(Never connectto more thantwo phasesat atime).
2)Note that it doesnotmatterwhich twowiresfromtheweldingmachineareconnectedto which two phasesat thistime; however,it will matter later when connectingthe ground wire(see Step5).
3)Connecta thirdwirefromtheweldingmachineto anotherphasein threephasebox or receptacle—again, it does not matterwhichphasethis wireis connectedto at this time.(Thiswill complete themakingof an electrical circuitand allowcurrent flowthroughtheweldingmachine.)
Ungrounded Delta Power Supply:
1)WARNING:UngroundeddeltapowersuppliesarenotcommonintheUnitedStatesandCanada;however,they maybeencounteredwhen working in other countries .When using an ungroundeddelta powersupply ,it is imperativethatyou take extreme caretoavoidelectricalshockhazards .
Small Welding Machine Wattage
Welding machines come in a variety of sizes, and their wattage output can vary widely. But what is the difference between a small welding machine and one with a higher wattage output?
The main difference between small welding machines and those with a higher wattage output is the amount of power they can provide.
Smaller welding machines typically have a lower maximum output than larger ones. This means that they can only provide enough power to weld thinner materials, or to make less powerful welds.
However, just because a welding machine has a lower wattage output doesn’t mean it’s not capable of doing good work.
In fact, many smaller welding machines are actually quite powerful and can be used for a variety of applications. It’s just that they’re not suitable for every job – like trying to weld thick metal plates together. For that, you’ll need something with more oomph!
300 Amp Welding Machine Wattage
A 300 amp welding machine is a powerful tool that can be used for a variety of welding projects. The wattage of this machine is 2000 watts, which makes it ideal for heavy-duty projects. This machine is also capable of running on both 110 and 220 volt power sources.
500 Amp Welding Machine Wattage
If you’re a welder, then you know that having the right welding machine is important. But what exactly does that mean? What are the specifications that you need to look for in a welding machine?
For most applications, a 500-amp welding machine with a wattage of at least 3,000 watts will be sufficient. This will allow you to weld metal thicknesses up to 1/2 inch. If you need to weld thicker metal, you’ll want a machine with more power.
When it comes to choosing a welder, there are many factors to consider. But if you’re looking for a versatile machine that can handle most projects, then a 500-amp model is a good place to start.
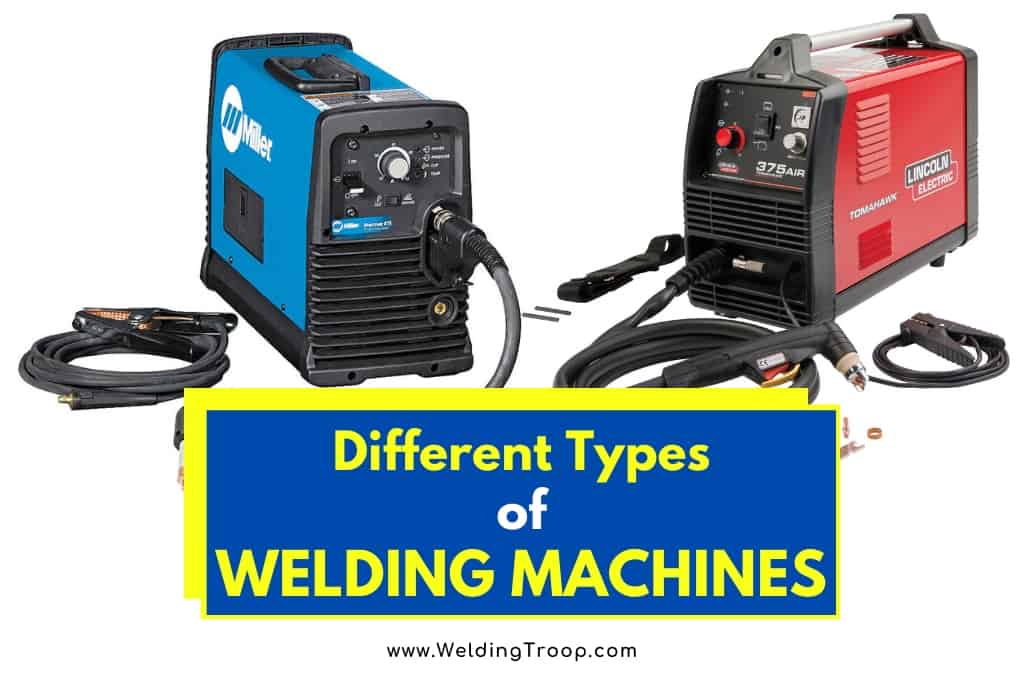
Credit: weldingtroop.com
How Do You Calculate Welding Cost?
Welding costs can be calculated in a number of ways, but the most common method is to calculate the cost per hour of welding. This can be done by taking the total cost of welding (labor, materials, overhead, etc.) and dividing it by the number of hours it took to complete the weld.
The total cost of welding includes both direct and indirect costs.
Direct costs are those that are directly related to the welding process, such as labor, materials, and gas. Indirect costs are those that are not directly related to welding but still need to be considered, such as overhead and depreciation.
To calculate the direct labor cost, you will need to know how many hours were spent welding and the hourly wage of the welder.
For example, if it took 10 hours to weld a part and the welder made $20 per hour, then the direct labor cost would be $200.
To calculate the cost of materials, you will need to know how much wire was used and how much gas was used. Wire is usually measured in pounds (lbs), while gas is often measured in cubic feet (cf).
For example, if 2 lbs of wire were used at a price of $3 per lb and 20 cf of gas were used at a price of $0.50 per cf , then the total material cost would be $22.50 .
The overhead rate is typically calculated as a percentage of direct labor costs. For example, if your overhead rate is 10%, then you would multiply your direct labor costs by 0.1 to get your overhead costs .
In our example above , this would mean that overhead would add an additional $20 to our total welding costs .
Depreciation can also play a role in calculating overall welding costs . If you own your own equipment , you will need to factor in depreciation expense when calculating your total hourly rate .
Adding all these factors together , we get a grand total estimated Welding Cost for our project :
Total Cost = Direct Cost + Indirect Cost + Depreciation
How Much Electricity Does a Welding Machine Use?
Welding machines are a vital piece of equipment in any metalworking shop. But how much electricity do they use?
The amount of electricity a welding machine uses depends on the type of machine and the welding process being used.
For example, an arc welder using AC current will use less electricity than a DC welder. Additionally, newer, more efficient machines may use less power than older models.
A typical 240-volt arc welder can draw up to 225 amps, which means it uses about 54 kilowatts of power. This is why welders must be connected to dedicated circuits that are not shared with other devices or appliances. If you’re thinking about getting a welding machine for your shop, make sure you have the proper electrical service to support it.
Otherwise, you may find yourself tripping circuit breakers or blowing fuses on a regular basis!
How Do You Calculate Welding Power?
Welding power is the amount of energy required to complete a welding process. It is typically measured in kilowatts (kW) or joules per second (J/s). There are a number of factors that can affect the welding power required for a given application, including the type of materials being welded, the thickness of those materials, the desired weld strength, and the welding speed.
In general, higher-power welding processes will be able to weld thicker materials or achieve stronger welds in less time than lower-power processes. Additionally, some welding processes may require more power when used on certain types of materials. For example, aluminum generally requires more power to weld than steel.
To calculate the approximate power required for your specific welding application, you can use this simple formula:
P = V x I x T / 1000
where: P = Power (in kW) V = Voltage (in volts) I = Current (in amps) T = Time (in seconds) / 1000 = Constant value to convert from amperes to kiloamperes
For example, let’s say you’re using a welding machine with an output voltage of 30V and an output current of 100A. You estimate that it will take you 60 seconds to complete your welding joint. Using the formula above, we can calculate that you’ll need approximately 18kW of power to complete your weld:
How Do I Calculate Amps for Welding?
Welding current is measured in amps. The welder’s output amperage must be set high enough to create a sufficiently hot arc, but low enough so that the welder does not overheat and trip its internal breaker.
The amount of heat needed to weld properly is determined by many factors, including the thickness of the metal being welded, welding position (flat, horizontal, or vertical), electrode type and diameter, and welding speed.
In general, you will want to set your welder’s output amperage at about 70% of the maximum it can produce for most applications. For example, if your welder has an output range of 40-225 amps, you would set it to around 140 amps for most projects.
Estimation of Welding Cost
Conclusion
If you are planning to buy a welding system, it is important to know the electric cost of the system. This will help you determine the overall cost of ownership and whether the system is affordable for your needs. There are a few things that you need to consider when calculating the electric cost of a welding system.
First, you need to determine the power rating of the machine. The power rating is typically expressed in watts or kilowatts (kW). You can find this information on the nameplate of the machine or in the specification sheet.
Once you have determined the power rating, you need to calculate the number of hours that the machine will be used per day. This information is important because it will be used to calculate your electricity usage charges.
Next, you need to find out your local electricity rate.
This information can be found on your utility bill or online at your local utility company’s website. Once you have determined your local electricity rate, you can multiply this number by the number of hours that the machine will be used per day to determine your daily electric cost.