If you’re looking to weld your exhaust system together, you may be wondering if an aluminum welding rod can be used. The answer is yes, but there are a few things to keep in mind. First, aluminum has a lower melting point than steel, so it will require less heat to weld.
This means that you’ll need to use a lower setting on your welder. Second, aluminum is more prone to oxidation than steel, so it’s important to clean the surfaces that you’re going to weld before starting. Finally, aluminum expands and contracts more than steel when heated, so it’s important to allow for expansion and contraction when welding exhaust systems made of aluminum.
An aluminum welding rod can be used on exhaust systems, but it is not the ideal material to use. Aluminum is a soft metal that is difficult to weld. It also corrodes easily and is not as strong as other metals.
If you must use an aluminum welding rod on your exhaust system, make sure to protect the area around the weld with a heat shield.
Can You Weld Aluminized Steel With Flux Core
Aluminized steel is a type of steel that has been coated with an aluminum-silicon alloy. This coating gives the steel increased resistance to corrosion and abrasion. While aluminized steel can be welded using standard welding methods, flux core welding is often the best choice for this type of metal.
Flux core welding is a type of welding that uses a wire electrode that is fed through a welding gun and into the weld pool. The electrode is surrounded by a flux compound that helps to shield the weld from contamination. This makes flux core welding ideal for outdoor applications or for welding metals that are difficult to clean, such as aluminized steel.
When welding aluminized steel with flux core, it’s important to use a low amperage setting on your welder. This will help to prevent the aluminum coating from burning off of the steel. It’s also important to use short arc lengths when welding, as this will help to avoid burn-through of the metal.
Mig Welding Aluminized Steel Exhaust
Mig Welding Aluminized Steel Exhaust
In the past, when welding aluminized steel exhaust systems it was recommended that you use a TIG welder. However, with advances in MIG welding technology, it is now possible to weld aluminized steel exhausts using a MIG welder.
When welding aluminized steel there are a few things that need to be taken into consideration:
1) Use Argon gas when welding- This will help to prevent the formation of oxides on the weld.
2) Set your machine for AC current- This will help to reduce or eliminate the risk of weld contamination.
3) Use thin walled tubing- Thicker walled tubing can cause issues with warping and distortion.
4) Use a short arc length- This will help to prevent excessive heat build up which can lead to premature failure of the weld.
Brazing Exhaust With Propane Torch
Brazing is a process of joining two pieces of metal together with a third, melted metal. It is similar to welding, but the temperatures required are much lower and there is no need for an external power source. Brazing can be done with a propane torch, making it a popular choice for do-it-yourself projects.
When brazing exhaust systems, it is important to use the proper flux and filler metals. The most common error made when brazing exhaust is using too much heat, which can cause the metal to warp or melt. If you are not experienced in brazing, it is best to seek professional help to avoid damaging your exhaust system.
Brazing Exhaust With Coat Hanger
Brazing exhaust with a coat hanger is a popular do-it-yourself method for repairing small holes in an exhaust system. This temporary fix can be completed in a few minutes and will hold up until you are able to replace the entire exhaust system. Here’s how to do it:
First, clean the area around the hole with sandpaper or a wire brush. This will help the coat hanger adhere to the metal.
Next, straighten out a wire hanger and cut off any sharp ends.
Then, feed the wire through the hole in the exhaust until there is about 6 inches sticking out on each side.
Now it’s time to start brazing. Heat up your torch and apply flux to both sides of the hole.
Then, touch the end of the wire hanger on each side of the hole to the molten flux – this will help conduct heat evenly across the joint. Finally, apply filler metal to one side of the joint and then use your torch to melt it into place. Continue doing this until you have filled in all of the voids around the hole.
Allow everything to cool before starting your engine!
Welding Aluminized Steel to Stainless
Welding aluminized steel to stainless is a process that can be used to create strong, reliable welds between two pieces of metal. The process is relatively simple and does not require any special equipment or training. However, there are a few things that you should keep in mind when welding these two metals together.
First, it is important to clean the surfaces of both pieces of metal before beginning the welding process. Any dirt, grease or other contaminants on the surface of either metal can cause problems with the welds. Second, it is best to use a filler material that is compatible with both aluminum and stainless steel.
This will help to ensure that the welds are strong and will not break easily. Finally, it is important to use proper welding techniques when joining these two metals together. If done correctly, the resulting weld will be strong and durable.
Tig Welding Aluminized Steel
Tig welding aluminized steel can be a challenge, but with the right technique it can be done successfully. Aluminized steel is steel that has been hot-dip coated with an aluminum-silicon alloy. This process gives the steel a bright, shiny finish and creates a barrier between the steel and the environment that helps to protect the steel from corrosion.
When welding aluminized steel, it is important to use an electrode that is compatible with the base metal. Incompatible electrodes can cause porosity and cracking in the weld. For best results, use an ER70S-6 or ER80S-D2 electrode.
When welding thin gauge material, it may be necessary to use a lower amperage setting on your welder to avoid burning through the material. If you are having trouble getting a good arc start on your aluminized steel, try using DCEN (direct current electrode negative) polarity instead of DCEP (direct current electrode positive). This will help to create a more stable arc.
Tig welding aluminized steel can be challenging, but with the right technique and equipment it can be done successfully.
Welding Aluminized Steel Fumes
Welding aluminized steel produces fumes that can be harmful to your health. The aluminum in the steel reacts with the oxygen in the air to create a fine powder that is easily inhaled. The particles are so small that they can pass through your lungs and enter your bloodstream.
This can lead to serious health problems, including cancer.
Second, work in a well-ventilated area. Third, use a fan to direct the fumes away from your face. Fourth, wear long sleeves and pants to protect your skin from the powder.
Fifth, wash your hands and face after welding to remove any residue. These precautions will help keep you safe while welding aluminized steel. Remember, it is always better to be safe than sorry when it comes to your health!
Can You Braze Stainless Steel Exhaust
You can braze stainless steel exhaust systems, but it is not as common as welding. Braze welding is a process where two pieces of metal are joined together with a brazing alloy. The brazing alloy melts at a lower temperature than the base metals, so it can be used to join dissimilar materials.
Stainless steel exhaust systems are usually welded because it is a stronger joint and can withstand higher temperatures.
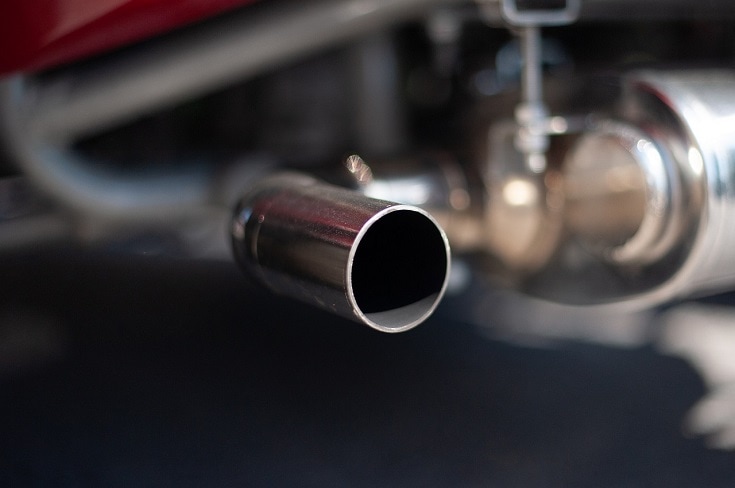
Credit: waterwelders.com
What is the Best Welding Rod for Welding Exhaust?
If you’re looking for the best welding rod for welding exhaust, you’ll want to consider a few key factors. Firstly, think about the material you’ll be welding. If you’re working with stainless steel or another difficult-to-weld metal, you’ll need a rod that can handle high temperatures and is specifically designed for that purpose.
Secondly, consider the thickness of the material you’ll be welding. The thicker the metal, the stronger and more durable the weld will need to be. Finally, take into account your own skill level and what kind of finish you’re hoping to achieve.
With these factors in mind, let’s take a look at some of the best welding rods on the market:
For thin metals:
The Lincoln Electric SuperGlaze ER4043 Aluminum MIG Welding Wire is our top pick for thin metals.
This wire is made from pure aluminum and provides excellent corrosion resistance thanks to its special flux coating. It also has great weldability properties, making it ideal for beginners or those with less experience in welding exhaust systems.
For thick metals:
If you’re dealing with thicker materials, we recommend going with the Hobart Fabshield 21B 10 lb Spool E71T-11 Flux-Cored Welding Wire . This wire is specifically designed for use with mild steel and comes in a handy 10lb spool size – perfect for larger projects. It produces low fume emission during welding thanks to its unique formula, making it ideal for use in well-ventilated areas or outdoors.
For stainless steel:
For those tricky stainless steel exhausts, we recommend using Hobart’s HB28 ER308L Stainless Steel MIG Welding Wire . This wire is made from austenitic stainless steel and contains 2% molybdenum which gives it superior corrosion resistance properties.
It’s also easy to weld with and produces clean results – perfect if you’re looking for a professional finish.
What Welding Rod is Good for Exhaust Pipe?
If you’re looking to weld an exhaust pipe, you’ll want to choose a welding rod that can withstand high temperatures. A good option is Inconel 625, which is a nickel-based alloy that’s resistant to corrosion and can handle temperatures up to 2000 degrees Fahrenheit. Another option is Hastelloy C-22, which has similar properties but can also withstand higher levels of chlorine and other chemicals that might be present in an exhaust system.
Whichever welding rod you choose, make sure it’s compatible with the metal you’re using for your exhaust pipe.
Can You Use a Stick Welder on Exhaust?
Most welders will tell you that it’s not a good idea to use a stick welder on exhaust. The main reason is that the heat from the welding process can cause the exhaust pipes to expand and warp. This can lead to serious problems with your vehicle’s exhaust system, and it can be very expensive to fix.
Another reason why you shouldn’t use a stick welder on exhaust is because the fumes from the welding process can be very dangerous. breathed in, these fumes can cause serious health problems, including cancer. So, it’s important to make sure that you have plenty of ventilation when you’re welding on your vehicle’s exhaust system.
If you absolutely must use a stick welder on your vehicle’s exhaust, there are some things you can do to minimize the risk of damage or injury. First, make sure that you’re using the lowest possible setting on your welder. Second, try to keep the welding area as small as possible.
And finally, make sure that you have plenty of ventilation so that you don’t breathe in any of the harmful fumes.
What Kind of Welder Do You Need for Exhaust Work?
If you’re looking to do some exhaust work and want to know what kind of welder you need, then read on. There are a few things to consider when choosing a welder for this type of work. The first is the thickness of the metal you’ll be working with.
If you’re working with thin gauge metal, then you’ll need a welder that can handle that. Another thing to consider is the type of welding you’ll be doing. If you’re just doing simple repairs, then an MIG welder will suffice.
However, if you’re looking to do more complex welds, then you might need an TIG welder. Finally, consider your budget and what features you need in a welder. With all that being said, let’s take a look at three different welders that would be good for exhaust work:
The first option is the Lincoln Electric Power MIG 210 MP Welder . This machine is capable of handling thin gauge metals and has both MIG and flux-cored welding capabilities. It also has Pulse-On-Pulse technology which provides better arc starts and improved weld bead control.
If budget is a concern, then this could be a good option for you as it’s one of the more affordable welders on the market.
The second option is the Miller Electric DYNAFlux -DFM Welder . This machine is specifically designed for thin gauge metals and offers excellent weld bead control thanks to its pulse width modulation feature.
It also has dual frequency capability which means it can operate at both 50Hz and 60Hz frequencies (which can be helpful if your power supply isn’t consistent). This makes it a great choice for those who want quality welds but don’t want to spend too much money.
The third option is the Hobart Handler 140 MIG Welder .
This machine is similar to the Miller Electric DYNAFlux -DFM Welder in terms of features and performance but comes in at a slightly lower price point. It’s perfect for those who are looking for an affordable yet reliable welder for their exhaust work needs.
Experimental aluminum welding procedure and it works
Conclusion
If you’re in a pinch and need to weld aluminum exhaust systems together, you can use an aluminum welding rod. Keep in mind that this is a temporary fix and not a permanent solution. The reason why this works is because the aluminum welding rod has a lower melting point than the steel exhaust system, so it will weld the two pieces together.