A2 tool steel is a versatile, all-purpose tool steel that can be used for a variety of applications. It has good hardenability and wear resistance, and is easy to weld. However, it can be difficult to weld A2 tool steel correctly, due to its high carbon content.
Here are some tips on how to weld A2 tool steel.
When it comes to welding A2 tool steel, the answer is yes – but with some caveats. This type of steel is often used for making cutting tools, as well as other applications where wear resistance and toughness are key. However, it can be difficult to weld due to its high carbon content.
Here are a few things to keep in mind if you’re considering welding A2 tool steel:
1. Use a low-carbon filler metal. Because A2 tool steel has a high carbon content, using a low-carbon filler metal will help to prevent cracks and other issues that can occur during the welding process.
2. Preheat the material before welding. This will help to reduce the risk of cracking and warping during Welding .
3. Use an appropriate gas mixture.
When welding A2 tool steel, it’s important to use an argon/carbon dioxide gas mixture in order to prevent porosity and other defects.
Tool Steel Welding Electrode
If you’re in the market for a new welding electrode, you may be wondering if tool steel is the right choice. Tool steel welding electrodes are designed for welding high carbon and alloy steels. They can be used on both AC and DC power sources, and they’re available in a variety of sizes and styles.
Tool steel welding electrodes offer several advantages over other types of electrodes. They provide excellent arc stability and penetration, making them ideal for welding thick or difficult-to-weld materials. They also produce minimal spatter and have a low burn-off rate, which means you’ll save money on consumables.
And because they’re made from tool steel, they’re less likely to break during use.
If you’re looking for a versatile, durable welding electrode that can handle even the most challenging projects, consider investing in a set of tool steel welding electrodes.
Welding Mild Steel to Tool Steel
Welding mild steel to tool steel can be done with any standard welding process, as both metals are easily welded. However, there are a few things to keep in mind in order to ensure a strong and reliable weld. First, it is important to use a low hydrogen electrode when welding these two metals together.
This will help to prevent cracking in the weld joint. Secondly, it is necessary to preheat the tool steel before welding. This can be done by heating the metal with an oxy-acetylene torch or by using an induction heater.
Preheating the metal will help to prevent warping and distortion during the welding process. Finally, it is important to post-heat the weld joint after welding in order to relieve stress on the joint and promote better weld strength.
A2 Tool Steel Tig Rod
A2 tool steel tig rod is a popular choice for welding and fabricating projects. This type of steel is known for its durability and resistance to wear. It is also easy to work with, making it a good choice for those new to welding or fabricating.
A2 tool steel can be used for a variety of applications, including automotive and aerospace parts, as well as knives and other cutting tools.
Welding Tool Steel
Welding is a process of joining two pieces of metal together by melting them and using a filler material to form a strong bond. Welding is often used to repair metal objects or to build structures from scratch. Welding can be done using various methods, including gas welding, arc welding, and resistance welding.
Tool steel is a type of steel that is designed for use in tools and machines. Tool steel is made from carbon and alloy steels that contain high levels of carbon. The higher the carbon content, the harder and tougher the tool steel will be.
Tool steel is used to make cutting tools, dies, and molds. It can also be used for other purposes such as forming and stamping metals.
When welding tool steel, it’s important to choose the right filler material.
The most common filler materials for tool steel are low-carbon steels, nickel-based alloys, or cobalt-based alloys. These materials will help to prevent weld cracking and improve the strength of the weld joint.
Welding W1 Tool Steel
Welding W1 tool steel is a process that can be used to join two pieces of this particular type of metal together. This process is different than other types of welding because it uses high heat to melt the metal, which allows it to fuse together more easily. There are three main methods that can be used when welding W1 tool steel: gas tungsten arc welding, plasma arc welding, and oxy-acetylene torch welding.
Each method has its own advantages and disadvantages, so it’s important to choose the right one for your project.
Gas tungsten arc welding, or GTAW, is also known as TIG welding. This method uses an electrode made of tungsten that is non-consumable, meaning it doesn’t melt during the welding process.
The heat needed to weld the metal is generated by an electric arc between the electrode and the metal itself. GTAW is often used on thin metals because it produces a clean weld with minimal distortion. However, this method can be more difficult to learn than other forms of welding and isn’t always well suited for large projects.
Plasma arc Welding (PAW) uses a plasma torch to create an electric arc between the electrode and the workpiece. The plasma gas heats up and ionizes when it comes into contact with the electric potential difference created by the electrode, which then melts the metal being welded. PAW is often used in automated systems because it’s a very precise form of welding that produces little slag or spatter.
However, like GTAW, PAW can also be difficult to learn and isn’t always well suited for large projects either. Oxy-acetylene torch Welding (OAW), also known as oxyfuel gas Welding (OFW), uses a flame from a burning mixture of oxygen and acetylene gases to weld two pieces of metal together. The flame created by OAW is much hotter than those produced by other methods like GTAW or PAW, which means that it’s capable of melting most metals quickly and easily.
However, OAW isn’t as precise as other methods since there’s no way to control exactly where the flame will hit the workpiece . It’s also important to note that OAW requires special training in order to use safely due too its highly combustible nature .
Welding D2 to Mild Steel
When it comes to welding D2 to mild steel, there are a few things you need to keep in mind. First of all, D2 is an extremely hard and tough tool steel, so it requires preheat and interpass temperatures that are higher than for other steels. Secondly, because of its high carbon content, D2 can be quite susceptible to cracking, so you need to take care to use the right welding procedures and techniques.
Assuming you have the necessary equipment and experience, welding D2 to mild steel is not overly difficult. The key is to use a filler metal that has a similar composition to D2 – such as 3% chromium or 9% nickel tool steel – and to apply generous amounts of heat during welding. Preheating the workpieces before welding is also essential, as this will help prevent cracking.
With proper care and attention, welding D2 to mild steel can be successfully accomplished without any major issues. Just remember to take your time, use the right materials and procedures, and apply plenty of heat throughout the process.
Welding S5 Tool Steel
Welding S5 tool steel can be a challenging process, but with the right tools and techniques it can be done successfully. Here are some tips to help you get started:
1. Choose the right welding rod.
S5 tool steel is best welded with a high carbon rod, such as an E7018 or E70S-6.
2. Preheat the metal before welding. This will help prevent cracking and warping during the welding process.
3. Use low amperage when welding S5 tool steel. Too much heat can damage the metal and make it difficult to work with. 4. Keep your welds clean and free of debris.
Any contaminants on the surface of the metal can cause problems during welding or affect the quality of the final weld joint.
Welding Hardened Steel
Welding hardened steel is not for the faint of heart. This is a difficult process that requires a great deal of skill and experience. However, if done correctly, welding hardened steel can be an incredibly strong and durable way to join two pieces of metal together.
There are a few things to keep in mind when welding hardened steel. First, it is important to use the correct type of electrode. Second, the amperage and voltage must be carefully controlled.
Third, it is necessary to preheat the area to be welded. Finally, post-weld heat treatment is required to relieve stress on the weld joint.
If you are considering welding hardened steel, make sure you have the skills and experience necessary to do so safely and correctly.
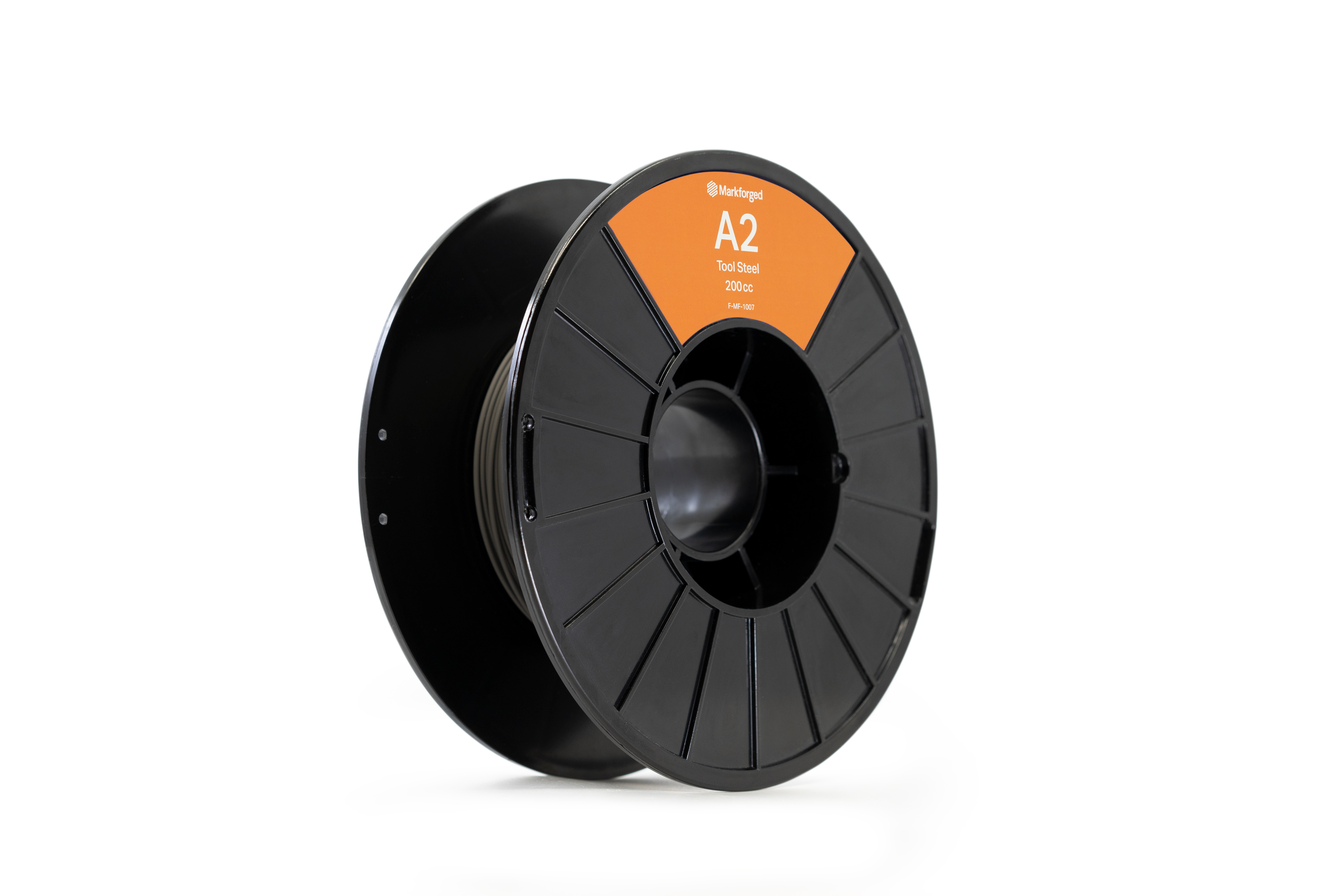
Credit: www.designfusion.build
Can Tool Steel Be Welded?
Yes, tool steel can be welded. However, because of its high carbon content and hardening properties, welding tool steel can be difficult and requires special techniques. For best results, consult a professional welder or metalworker.
Is A2 Steel Strong?
A2 steel is an air hardening tool steel that is often used in power tools and knives. It is a very tough steel with a high wear resistance, making it ideal for cutting and grinding applications. A2 steel also has a good corrosion resistance and can be heat treated to increase its hardness.
Can You Weld D2 Tool Steel?
Yes, you can weld D2 tool steel. However, it is important to note that this type of steel is not ideal for welding and can be difficult to work with. When welding D2 tool steel, it is important to use a low heat setting and avoid overheating the metal.
It is also important to use a filler material that is compatible with the metal.
What is A2 Steel Used For?
A2 tool steel is an air hardening, cold work, chromium alloy die steel that is preferred for light to moderate wear applications. A2 is characterized by good machinability, good toughness, excellent wear resistance and high hardness. It also has a lower carbon content than most other tool steels which gives it better weldability.
TIG Welding with TOOL STEEL filler?!
Conclusion
Tool steels are extremely hard and are difficult to weld. However, with the right equipment and welding techniques, it is possible to weld tool steel. In this blog post, we will discuss how to weld A2 tool steel, including the best filler metals and welding methods to use.