There are a variety of clamps that can be used for tack welding, which is a type of welding that is used to hold two pieces of metal together temporarily. The most common type of clamp used for tack welding is the C-clamp, which is a simple device that consists of two jaws that are connected by a screw. Other types of clamps that can be used for tack welding include magnetic clamps, vise grips, and pipe clamps.
Each type of clamp has its own advantages and disadvantages, so it is important to choose the right clamp for the job at hand.
If you’re new to tack welding, you might be wondering what kind of clamps you can use. The good news is that a variety of clamps can be used for tack welding! This means that you can find the perfect clamp for your project, whether it’s a small or large scale project.
Some of the most popular clamps for tack welding include C-clamps, F-clamps, and G-clamps. Each of these clamps has its own unique benefits that make them ideal for tack welding. For example, C-clamps are great for small projects because they provide a tight grip without being too bulky.
F-clamps are perfect for larger projects because they offer more stability and support. And finally, G-clamps are ideal for both small and large projects because they offer a versatile grip that can be adjusted to fit your needs.
So whatever type of project you’re working on, there’s a clamp out there that will work perfectly!
Just do some research and figure out which one is right for you.
Tack Welding Procedure Pdf
Tack welding is a quick and easy way to join two pieces of metal together. It’s often used to hold pieces in place while more permanent welds are made, or to weld together parts that will be disassembled later.
The key to successful tack welding is to use short, quick welds.
If the welds are too long or slow, they can cause warping or other problems. Here’s a step-by-step guide to tack welding:
1. Clean the metal surfaces that will be joined.
Remove any rust, paint, oil, or other contaminants.
2. Position the two pieces of metal so that they’re flush against each other. Clamp them in place if necessary.
3. Select the right electrode for your welder and set the machine to the appropriate settings. For most applications, a mild steel electrode with a gasless flux core wire works well.
4.”Strike” an arc by touching the tip of the electrode to the metal and then quickly withdrawing it.
The arc should be about 1/8 inch long. If it’s too long or too short, adjust the power settings on your welder accordingly.
5.”Weave” the arc back and forth across the joint as you slowly move down its length.
Maintain a consistent speed and width for best results.”Tie off”the end of your weld by running the bead off the edge of one piece of metal onto the other piece.”Break”the arc by quickly moving the electrode away from both pieces of metal.
“Dip”the end of your electrode into water to cool it off before starting another tack weld.]
3 Kinds of Tack Welding
Tack welding is a process that is used to weld two pieces of metal together. There are three main types of tack welding: MIG, TIG, and Stick.
MIG tack welding is done with a MIG welder.
This type of tack welding is best for thin metals because it can be difficult to control the heat when using a MIG welder. When tack welding with a MIG welder, it is important to use short bursts of weld so that the heat does not build up too much and cause warping.
TIG tack welding is done with a TIG welder.
This type of tack welding is best for thicker metals because it allows for more control over the heat. Tack welding with a TIG welder requires more skill than MIG tack welding because you have to be able to maintain a steady arc while moving the torch around the joint.
This type of tack welding is best for thick metals because it produces a lot of heat and can penetrate deeply into the metal.
Types of Tack Welding
There are three types of tack welding: spot welding, seam welding, and butt welding. Each type has its own advantages and disadvantages, so it’s important to choose the right one for your project.
Spot Welding
Spot welding is the most common type of tack weld. It’s quick and easy to do, and it produces a strong weld joint. However, spot welding can only be used on thin materials.
If you’re working with thicker materials, you’ll need to use a different type of tack weld.
Seam Welding
Seam welding is similar to spot welding, but it’s used on thicker materials.
Seam welding produces a stronger weld joint than spot welding, but it’s also more difficult to do. You’ll need to have a good understanding of how to set up your equipment before you attempt this type of tack weld.
Butt Welding
Butt welding is the strongest type of tack weld. It’s also the most difficult to do, and it requires special equipment. Butt welding is usually only done by experienced welders.
If you’re not sure what you’re doing, you shouldn’t attempt this type of tack weld.
Tack Weld Vs Spot Weld
If you’re working with metal, chances are you’ll need to weld at some point. But what kind of welding should you use? Tack welding and spot welding are two common options, but which one is best for your project?
Let’s take a closer look at tack welding vs spot welding so you can make the best decision for your next project.
What Is Tack Welding?
Tack welding is a type of welding that is used to temporarily hold two pieces of metal together.
It’s not meant to be a permanent connection, but it can be used to hold pieces in place while you work on making a more permanent connection.
Tack welds are usually small and quick to create. They’re also typically not as strong as other types of welds, which is why they’re only meant to be temporary.
However, tack welds can be useful if you need to quickly connect two pieces of metal or if you’re working in a difficult-to-reach area.
What Is Spot Welding?
Spot welding is another type of welding that is commonly used with metals.
Unlike tack welding, spot welding creates a permanent connection between two pieces of metal. Spot welds are usually stronger than tack welds since they’re meant to be permanent.
What Type of Clamp Should Be Used to Apply Pressure Over a Wide Area?
Whether you are working in the woodshop or on a construction site, there are times when you need to apply pressure over a wide area. In these cases, using the right type of clamp is essential to getting the job done correctly. Here is a look at some of the different types of clamps that can be used for this purpose, as well as some tips on how to choose the right one for your needs.
Bar Clamps: Bar clamps are one of the most versatile types of clamps and can be used for a variety of tasks. They have long bars that allow you to apply pressure over a wide area, and they come in both standard and deep-throat varieties. Standard bar clamps are great for general purpose use, while deep-throat clamps are ideal for situations where you need more reach.
Pipe Clamps: Pipe clamps are another option for applying pressure over a wide area. They have shorter bars than bar clamps, but they make up for it with their adjustable jaws. This makes them perfect for clamping irregularly shaped objects or materials that need to be held together tightly.
C-Clamps: C-clamps are similar to bar clamps, but they have shorter bars and smaller jaws. This makes them better suited for light duty tasks or projects where space is limited. However, they can still be used to apply pressure over a wide area if necessary.
Webbing Clamp: Webbing clamps are designed specifically for applying pressure over webbing or other fabric materials. They have serrated jaws that grip the material firmly without damaging it, making them ideal for delicate projects like upholstery work. Choosing the right type of clamp is important when you need to apply pressure over a wide area.
Consider what kind of project you will be working on and select a clamp accordingly. With so many options available, you’re sure to find one that’s just right for the task at hand!
5 Types of Clamps
There are many different types of clamps, each with their own specific uses. Here are five of the most common types:
1. G Clamps – also known as C-clamps or woodworking clamps, these are the most versatile type of clamp and can be used for a variety of tasks such as holding together two pieces of wood while glue dries, or securing a workpiece to a table during sawing or drilling.
2. F Clamps – also called bar clamps, these have longer jaws than G clamps and so can be used to clamp larger workpieces. They are particularly useful for cabinetsmaking and other woodworking tasks where long, straight edges need to be held together firmly.
3. Sash Clamps – these have shorter jaws than G or F clamps but are much longer overall, making them ideal for clamping long boards or sheets of material such as plywood.
They are often used in boatbuilding and other similar applications.
4. Pipe Clamps – as the name suggests, these clamps are designed specifically for use with pipes and tubing. They come in various sizes to accommodate different diameters of pipe, and can be used to secure pipes in place during welding or soldering operations.
5. Spring Clamp – this is a small clamp with springs instead of screws or nails which holds it closed.
Sanitary Tube Tacking Clamps
If you are in the market for sanitary tube tacking clamps, you have come to the right place. This blog post will provide detailed information about these types of clamps so that you can make an informed decision about which ones are right for your needs.
Sanitary tube tacking clamps are used to secure sanitary tubing in place.
There are many different types and sizes of sanitary tube tacking clamps available on the market, so it is important to know what your options are before making a purchase. The most common type of sanitary tube tacker is the worm drive clamp, which uses a screw-type mechanism to tighten or loosen the clamp around the tubing. Other types of sanitary tube tackers include pinch clamps, which use a spring-loaded mechanism to secure the tubing, and capstan clamps, which use a ratcheting mechanism to tighten or loosen the clamp.
When choosing a sanitary tube tacker, it is important to consider the size and type of tubing that you will be using it with. Some models are designed for specific types of tubing, such as PVC or stainless steel. Others are universal and can be used with any type of tubing.
It is also important to consider how often you will need to use the clamp and whether you need a model that can be adjusted for different diameters of tubing.
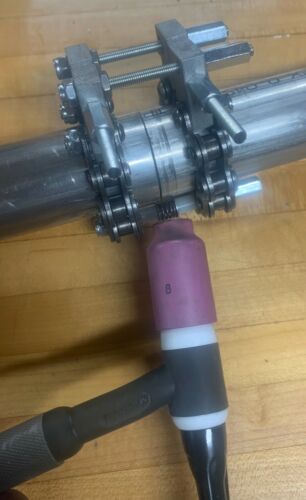
Credit: www.ebay.com
What Clamps to Use for Welding?
When it comes to welding, there are a variety of clamps that can be used in order to secure the materials being worked on. The type of clamp that you use will depend on the specific application and the materials being used. Some of the most common types of clamps include:
Welding magnets: These clamps are specifically designed for holding metal pieces together during welding. They are typically made from high-strength magnets that can hold even heavy pieces of metal in place.
C-clamps: C-clamps are one of the most versatile types of clamps and can be used for a variety of applications, including welding.
They get their name from their shape, which resembles a “C” when viewed from the side. These clamps can be adjusted to fit different sizes of material and have a wide range of uses beyond welding.
They typically have jaws that open up to accommodate different diameters of pipe and then tighten down to hold it securely in place. Bar clamps: Bar clamps are another versatile type of clamp that can be used for various applications, including welding. They consist of two jaws connected by a bar, which allows them to be adjusted to fit different sizes of material.
Like C-clams, they get their name from their shape when viewed from the side – they resemble a capital “I” beam when viewed this way.
What are 3 Types of Bar Clamps?
There are three types of bar clamps: pipe clamp, spring clamp, and ratchet clamp.
Pipe Clamp: A pipe clamp is a type of clamp that is used to secure a pipe to a work surface. This type of clamp is typically used in woodworking or metalworking.
The jaws of the clamp are adjustable so that it can grip different sizes of pipes.
Spring Clamp: A spring clamp is a type of clamp that uses springs to create tension. This type of clamp is often used in woodworking or metalworking.
The tension created by the springs helps to keep the jaws of the clamp tight against the workpiece.
Ratchet Clamp: A ratchet clamptype of clamthat uses a ratcheting mechanism to create tension. This typeof clamis oftenusedin woodworkingor metalworking .
The ratcheting mechanism helps to keep the jaws ofthe clamptight againstthe workpiece .
How Many Types of Tack Welding There Is?
There are four main types of tack welding: spot welding, seam welding, butt welding, and flash welding. Spot welding is the most common type of tack weld and is used to join two pieces of metal together at a small, specific area. Seam welding is similar to spot welding but is used to join two pieces of metal along a seam or edge.
Butt welding joins two pieces of metal together at their ends. Flash welding joins two pieces of metal together by passing an electric current through them and then quickly cooling them with water or air.
What are Different Types of Clamps?
Different types of clamps are typically used for different purposes. Some common types of clamps include:
-Bar clamps: these are typically used for woodworking projects, and have a bar that can be tightened or loosened to adjust the clamping pressure.
-C-clamps: these are usually smaller and more compact than bar clamps, making them ideal for use in tighter spaces. They also have a screw mechanism that allows for precise adjustment of clamping pressure.
-Pipe clamps: as the name suggests, these clamps are designed specifically for use with pipes.
They usually have a large jaws that can accommodate different sizes of pipe, and they may also have an adjustable jaw to apply more or less pressure as needed.
TFS: The Coolest Stick Welding Tacking Trick I Learned
Conclusion
While most people think of welding as a process that uses heat to join two pieces of metal together, it’s actually possible to weld without using any heat at all. This process is called tack welding, and it’s often used when two pieces of metal need to be temporarily joined together. Tack welding can be done with a variety of clamps, including C-clamps, F-clamps, and G-clamps.
Each type of clamp has its own advantages and disadvantages, so it’s important to choose the right clamp for the job at hand. C-clamps are the most commonly used type of clamp for tack welding. They’re inexpensive and easy to use, but they don’t provide as much holding power as other types of clamps.
F-clamps are more expensive than C-clamps, but they offer more holding power and are less likely to slip during use. G-clamps are the most expensive type of clamp, but they offer the best holding power and are unlikely to slip or come loose during use.