Argon is a gas that is used in welding systems because it helps to create an environment where welding can take place. Argon is used because it is non-reactive, which means that it will not react with the other elements that are being used in the welding process. This gas also has a high density, which means that it can help to protect the weld from oxidation.
Welding is a process of joining two materials together by heating them to their melting point and then cooling them so that they solidify as one. In order for welding to be successful, the materials being joined must be compatible and have a similar composition. One of the most important elements in welding is argon.
Argon is an inert gas that makes up approximately 1% of the earth’s atmosphere. It is colorless, odorless, and non-flammable. Argon is used in welding because it protects the weld area from oxygen and other atmospheric gases that can contaminate the weld pool and cause porosity (tiny holes) in the weld.
When argon is used in welding, it forms a “shield” around the weld area. This shield prevents oxygen and other atmospheric gases from coming into contact with the hot weld pool. Argon also helps to stabilize the arc, which results in a smoother, more consistent bead appearance on the finished weld.
While argon is not required for all types of welding, it is often used in tungsten inert gas (TIG) welding and metal active gas (MAG) welding processes. When used properly, argon can help produce high quality welds that are strong and free of defects.
What is Argon Used for
Argon is a gas that is used in many different industries. It is often used as an inert gas, meaning it does not interact with other elements. This makes it ideal for use in welding and other industrial applications where there is a risk of fire or explosion.
Argon is also used in incandescent light bulbs and fluorescent lights.
Argon is Used As a Solvent
Argon is a noble gas that is used in many different ways. One of those ways is as a solvent. Argon is an excellent solvent because it does not react with most materials, it has a very low boiling point, and it is non-flammable.
These properties make argon ideal for use in many different industries. Argon is used as a solvent in many different applications. One example is in the production of semiconductors.
Argon is used to clean the surfaces of semiconductor wafers before they are coated with silicon dioxide. This process removes impurities from the surface of the wafer, which improves the quality of the finished product. Another example where argon is used as a solvent is in the printing industry.
Inks are typically made up of pigments suspended in a liquid carrier. Argon can be used to replace the carrier fluid in some ink formulations. This results in a more concentrated ink that can be printed at higher resolutions without clogging printer nozzles.
There are many other examples of where argon can be used as a solvent. These are just two examples of how this versatile gas can be put to good use!
Argon Welding Process
Argon welding is a type of welding that uses an inert gas to shield the weld from contamination. This process can be used for both ferrous and non-ferrous metals. Argon is the most common gas used for this purpose, but other gases such as helium or nitrogen can also be used.
The argon welding process works by using an electric arc to heat the metals being joined. As the metal melts, a filler material is added to create a new joint. The molten metal then cools and hardens, creating a strong bond between the two pieces of metal.
One advantage of argon welding over other methods is that it produces very little smoke or fumes. This makes it ideal for use in enclosed spaces or areas where ventilation is limited. Argon welding also produces less spatter than other methods, making it easier to achieve a clean finish on your project.
If you’re looking for a versatile welding method that can be used on a variety of materials, argon welding may be the right choice for you. Give it a try today and see how easy and effective it can be!
Argon Welder Salary
An argon welder is responsible for welding metal using an electric arc. They must have a strong understanding of the properties of metals and how they react to heat. In addition, they must be able to operate various welding machines and tools.
The average salary for an argon welder is $30 per hour. However, salaries can range from $25-$35 per hour, depending on experience and location.
Argon Welding Safety
Argon welding is a safe and effective way to weld metals together. However, there are some safety precautions that you should take when using this type of welding process. Here are some tips to help you stay safe while argon welding:
Wear the proper safety gear – When argon welding, it is important to wear the proper safety gear. This includes a face shield, gloves, and protective clothing. Use the right tools – Make sure that you are using the right tools for the job.
This includes an Argon welder and the appropriate consumables. Follow directions – Be sure to follow all directions when argon welding. This will help ensure that the job is done safely and correctly.
Argon Gas Welding Side Effects
Argon gas welding, also known as metal inert gas (MIG) welding, is a popular type of welding that uses an argon gas mixture to protect the weld area from oxidation. While argon gas welding has many benefits, there are also some potential side effects that welders should be aware of. One of the most common side effects of argon gas welding is eye irritation.
The bright light generated by the welding arc can cause temporary blindness and/or damage to the retina. To protect your eyes while argon gas welding, it is important to wear proper eye protection, including a face shield or goggles with dark lenses. Another potential side effect of argon gas welding is skin irritation.
The ultraviolet light generated by the welding arc can cause burns on exposed skin. To protect your skin while argon gas welding, it is important to wear proper protective clothing, including gloves, long sleeves, and pants. Inhaling Argon Gas Welding fumes can also be harmful to your health.
Argon gas itself is not toxic; however, it can displace oxygen in the air and lead to asphyxiation. In addition, other gases present in the argon mixture (such as carbon dioxide and nitrogen oxide) can be harmful if inhaled in high concentrations. To protect yourself from these dangers while argon gas welding, it is important to work in a well-ventilated area and use a respirator if necessary.
Argon Welding Vs Tig Welding
Welding is a process of joining two pieces of metal together by heating them to a molten state and then cooling them so that they form a strong bond. There are many different types of welding, but argon welding and TIG welding are two of the most popular. So, what’s the difference between these two methods?
Argon welding, also known as gas tungsten arc welding (GTAW), is a type of welding that uses an arc between a non-consumable tungsten electrode and the workpiece to create heat. The weld area is protected from oxidation by an inert gas, such as argon or helium. This makes argon welding ideal for thin materials or metals that are sensitive to oxidation, like aluminum.
TIG welding, on the other hand, stands for tungsten inert gas welding. It’s similar to argon welding in that an arc is used to create heat between a tungsten electrode and the workpiece. However, in TIG welding, the filler material is added manually to the weld area instead of being fed through the electrode like in GTAW.
This gives you more control over the weld bead shape and size. Additionally, TIG can be used on a wider range of materials than GTAW since there’s no need for an inert gas shield around the weld area. So which method should you use?
It really depends on your project and what material you’re working with. If you need precise control over the weld bead or if you’re working with materials that are sensitive to oxidation, then argon Welding would be your best bet. However, if you’re looking for more versatility or want to avoid using shielding gases altogether, then TIG might be better suited for your needs.
Argon Welding Video
Welding is a process of joining two pieces of metal together by using heat and pressure. The most common type of welding is argon welding. In this process, an electric arc is used to create the heat necessary to melt the metals.
A gas, typically argon, is used to shield the weld from oxygen and other contaminants in the air. There are many advantages to using argon welding. One advantage is that it creates a stronger bond than other types of welding.
Another advantage is that it’s less likely to create defects in the welded joint. Finally, argon welding can be used on a variety of different metals, including aluminum and stainless steel.
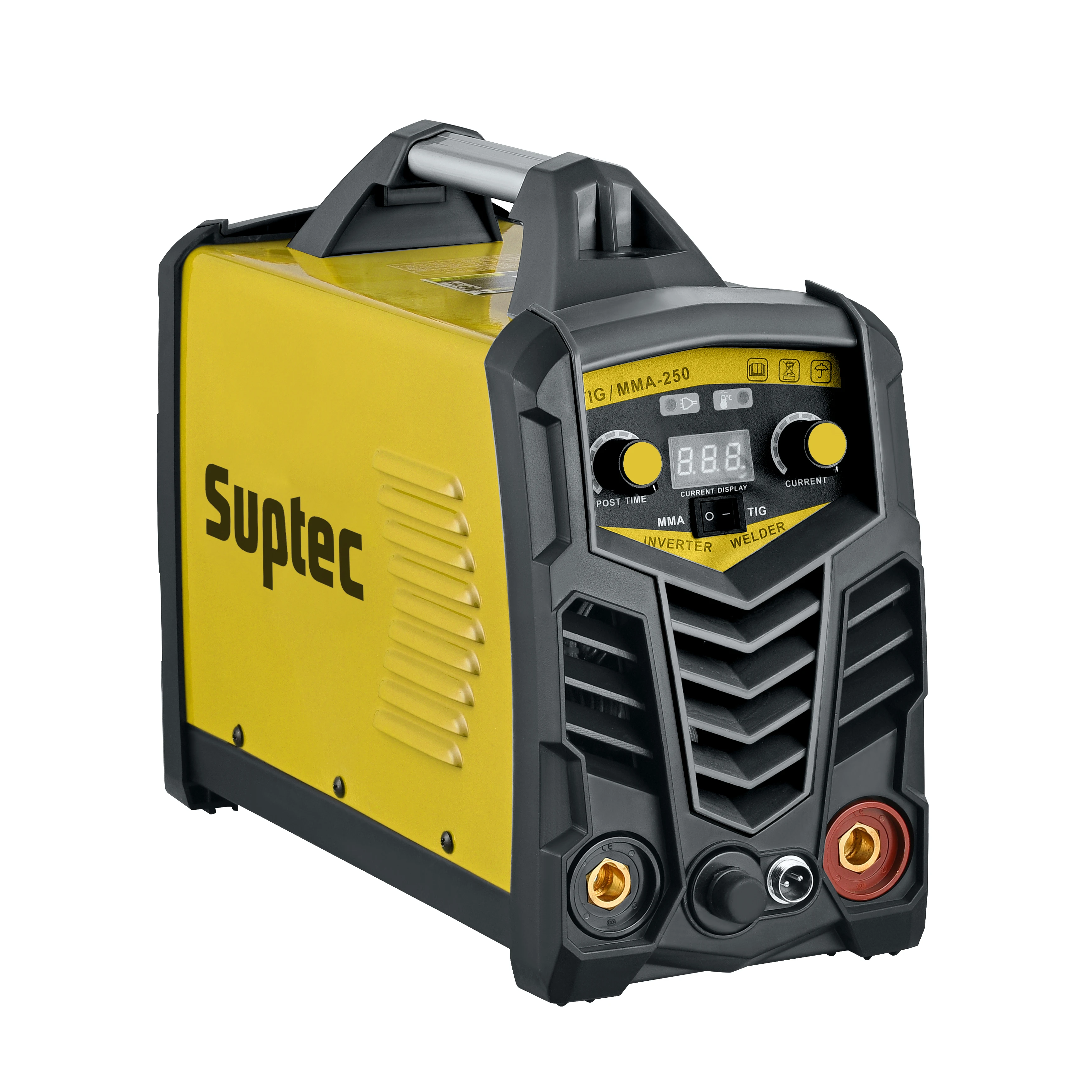
Credit: www.alibaba.com
Where Do We Use Argon Welding?
Argon welding is a gas welding process that uses an argon gas shield. The argon gas shield protects the weld area from atmospheric contamination, which can cause porosity and other defects. Argon welding is commonly used in applications where a high degree of weld purity is required, such as in the food and beverage industry.
Which Welding is Done by Argon Gas?
Welding is a process of joining two pieces of metal together by using heat and pressure. There are various types of welding, but one that is done using argon gas is called tungsten inert gas (TIG) welding. This type of welding is often used for thin metals, such as aluminum or stainless steel.
Argon gas is used in TIG welding because it helps to create an electric arc between the tungsten electrode and the metal being welded. The arc creates heat that melts the metal, allowing the two pieces to be joined together. TIG welding can be done with or without filler material.
When filler material is used, it is added to the joint area before welding begins. This helps to create a stronger bond between the two pieces of metal. Overall, TIG welding is a very versatile type of welding that can be used on a variety of materials.
It does require some practice to master, but once you get the hang of it, you’ll be able to produce high-quality welds time and time again.
Mig welding with Argon and Co2 [ Etch Testing]
Conclusion
Argon is used in welding systems for several reasons. First, it is an inert gas, meaning that it does not react chemically with other elements. This makes it ideal for protecting welds from contamination.
Second, argon is less dense than air, so it helps to create a more stable arc during welding. Finally, argon is relatively inexpensive and readily available, making it a popular choice for welding applications.