The work clamp is the part of a welding machine that connects to the workpiece. It helps to complete the circuit between the power source and the electrode. The current from the electrode passes through the work clamp to create an arc between the electrode and the workpiece.
This arc melts the metal, which forms a weld bead.
Are you looking for a way to attach your workpiece to your welding table? If so, then you may be wondering where does work clamp attach weld. The answer is that it depends on the type of welding you are doing.
For example, if you are doing MIG welding, then the work clamp will typically attach to the ground terminal on your welder. On the other hand, if you are doing TIG welding, then the work clamp will typically attach to the Positive (P) terminal on your welder. So, where does work clamp attach weld?
It really depends on the type of welding you are doing. Just be sure to consult your welder’s manual for specific instructions on where to attach the work clamp for your particular welding application.
Welding Ground Clamp Purpose
Welding ground clamps are an essential part of any welder’s toolkit. They provide a safe and easy way to attach a welding electrode to a workpiece, ensuring that the electrical current has a path to flow through. Ground clamps also help protect the welder from electrical shock.
There are two main types of welding ground clamps: copper and aluminum. Copper ground clamps are the most common type, as they offer good conductivity and durability. Aluminum ground clamps are lighter in weight and can be easier to maneuver, but they may not provide as strong of a connection.
When choosing a welding ground clamp, it is important to select one that is sized appropriately for the job at hand. Smaller projects may only require a lightweight aluminum clamp, while larger jobs will need a more heavy-duty copper clamp. It is also important to consider the material being welded; some metals will require special grounding techniques in order to avoid damage during the welding process.
No matter what type or size of welding ground clamp you choose, always be sure to follow safety guidelines when using them. Never leave an electrode unattended while it is still hot, and always wear protective clothing and equipment when welding. With proper care and use, your welding ground clamp will last for many years of successful projects!
Welding Ground Cable
Welding ground cables are an essential part of any welder’s toolkit. They provide a path for electricity to flow from the welding machine to the workpiece, and help to ensure a consistent, high-quality weld. Here’s everything you need to know about welding ground cables, including how to select the right one for your needs.
When it comes to welding, having a good ground is crucial. A welding ground cable provides a low-resistance path back to the power source so that current can flow freely during welding. This helps ensure a consistent, high-quality weld.
There are many different types of welding ground cables on the market, so it’s important to select the right one for your needs. The most important factors to consider are amperage rating, length, and diameter. The amperage rating of a welding ground cable corresponds to the maximum amount of current that it can safely carry.
It’s important to choose a cable with an amp rating that matches or exceeds the output of your welder. Length and diameter also play a role in determining how much current a cable can carry – longer and/or thicker cables will have higher amp ratings than shorter or thinner ones. Once you’ve selected a suitable welding ground cable, be sure to follow all manufacturer instructions regarding installation and use.
With proper care, your new cable should provide years of reliable service.
Welding Ground Clamp Upgrade
If you’re a welder, then you know that having a good ground clamp is essential. A ground clamp helps to ensure that your welds are of the highest quality possible. There are a few different factors that you should consider when upgrading your ground clamp.
The first is the size of the jaws. You’ll want to make sure that the jaws are large enough to fit around the metal that you’re welding on. If they’re too small, then it will be difficult to get a good connection.
Another important factor is the material of the jaws. You’ll want to make sure that they’re made from a durable material that can withstand high temperatures. The last thing you want is for your ground clamp to break in the middle of a weld!
You also need to consider the length of the cable. A longer cable gives you more flexibility when welding, but it also means that there’s more opportunity for the cable to get tangled up. If you’re constantly having to stop and untangle your cable, then it might be worth opting for a shorter one.
Finally, you need to think about how much power your ground clamp can handle. If you’re only going to be using it for light-duty welding jobs, then there’s no need to invest in an industrial-strength model. However, if you plan on doing some heavy-duty welding, then make sure you choose a ground clamp that can handle the load!
Stick Welding Ground Positive Or Negative
Welding is a process of joining two pieces of metal together by heating them until they melt and then cooling them so that they solidify as one piece. There are many different welding processes, but one of the most common is stick welding. In stick welding, an electrode (a metal rod) is used to create an arc between the metals being joined.
The heat from this arc melts the metals, allowing them to be joined together. One of the most important aspects of stick welding is ground polarity. This refers to whether the electrode is connected to the positive or negative side of the power source.
If the electrode is connected to the positive side, it’s called “positive polarity.” If it’s connected to the negative side, it’s called “negative polarity.” Most welders will use positive polarity when welding steel because it provides more penetration into the metal.
However, negative polarity can be used for some applications where less penetration is desired, such as when welding aluminum or stainless steel. If you’re not sure which ground polarity to use for your project, consult a professional welder or read your machine’s manual for guidance.
Where to Ground When Welding Exhaust
When welding on a vehicle exhaust, it is important to ground the metal properly to avoid any potential issues. The best way to do this is to use a ground clamp that is designed specifically for automotive work. This type of clamp will have a strong hold on the metal and will not slip or come loose while you are working.
If you do not have a ground clamp, you can still ground the metal by using a piece of bare copper wire. Wrap the wire around the exhaust pipe and then secure it in place with tape or zip ties. Once the wire is in place, simply touch it to the welding electrode to create a good connection.
Mig Welding Ground Positive Or Negative
Mig welding is a type of welding that uses an electric arc to create heat. The heat is then used to melt metal, which is then joined together. There are two types of mig welding: ground positive and ground negative.
Ground positive mig welding means that the electrode (the part of the machine that emits the arc) is connected to the work piece, and ground negative mig welding means that the electrode is connected to the power source. Each has its own advantages and disadvantages. Ground positive mig welding is easier to learn because it doesn’t require as much finesse.
The arc is also less likely to wander, making it ideal for beginners. However, ground positive mig welding can cause welds to be weaker and less aesthetically pleasing than ground negative welds. Ground negative mig welding produces stronger welds because the arc is hotter.
This method also gives you more control over the direction of the arc, making it easier to produce cleaner welds. However, ground negative mig welding can be harder to learn because it requires more precision and practice to master.
What Happens If You Don’T Ground a Welder
If you don’t ground a welder, the welder can create an electrical current that flows through your body. This current can cause burns, muscle spasms, and even heart failure.
Ground Clamp Welding Definition
A ground clamp is a tool that is used to create a temporary connection between a metal object and the ground. This connection allows for the safe and efficient welding of the object to the ground. The ground clamp is an important part of the welding process, as it ensures that all of the electricity from the welder is transferred safely into the ground instead of into the person who is welding.
There are two main types of ground clamps: those that use jumper cables and those that do not. Jumper cable clamps have two sets of jaws, one set for each cable, which grip onto the workpiece and allow for a secure connection. Non-jumper cable clamps typically have only one set of jaws and are attached directly to the workpiece without the use of cables.
Ground clamps are an essential piece of equipment for any welders, as they provide a safe way to transfer electricity during the welding process. Without a ground clamp, there would be a risk of electrical shock or fire if something went wrong with the weld. If you are planning on doing any welding, be sure to invest in a good quality ground clamp so that you can work safely and efficiently.
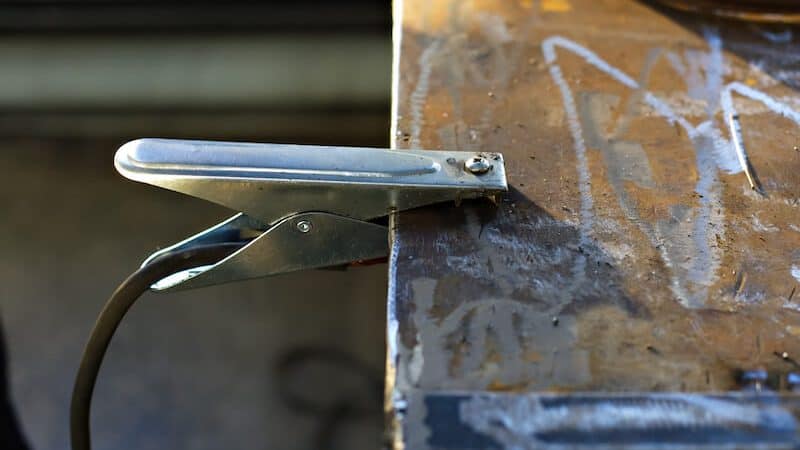
Credit: weldguru.com
Where Does the Clamp Go When Welding?
When welding, the clamp is placed around the two pieces of metal that are being joined together. This helps to hold them in place and prevent them from moving while you weld. It is important to make sure that the clamp is tight enough so that it does not slip, but not too tight so that it constricts the metal and prevents you from welding properly.
What is Work Clamp in Welding?
Work clamp in welding is a device that is used to hold the workpiece in place during welding. It is usually made of metal and has a jaws that open and close to grip the workpiece. The work clamp is connected to the power source and provides the electrical current that is needed for welding.
Where Does the Welder State is the Best Place to Put the Ground Clamp?
There are a few things to consider when determining where to place the ground clamp for welding. The first is the type of welding being done. If stick welding, the ground clamp should be placed as close to the work piece as possible.
This helps to ensure a good connection and allows for better arc control. If MIG or TIG welding, the ground clamp can be placed further away from the work piece since these types of welding use an electrode that is not in contact with the work piece. Another thing to consider is the material being welded.
If welding something like aluminum, which has a higher electrical conductivity than steel, it’s important to place the ground clamp closer to the work piece so that more heat is transferred into the work piece and less into the ground cable. This will help prevent burns and damage to both the work piece and ground cable. The last thing to consider is personal preference and comfort.
Some welders prefer to have the ground clamp close by so they can easily reach it if needed, while others find it more comfortable to have it further away. Ultimately, it’s up to the welder to decide where they feel most comfortable placing their ground clamp.
What is the Function of the Work Clamp?
The work clamp is an important part of the welding process. It helps to hold the workpiece in place so that it can be welded properly. Without a work clamp, the welding process would be much more difficult and could result in poor welds.
The work clamp is usually made from a strong material such as steel or aluminum. It is placed on the workpiece before welding begins. The welder then uses the work clamp to hold the workpiece in place while he or she welds it.
The work clamp helps to keep the workpiece from moving around during welding. This is important because it can help to prevent accidents and ensure that the welds are of good quality. Welders need to be very careful when using a work clamp.
If it is not used correctly, it can cause problems with the welding process. For example, if the wrong type of material is used for the work clamp, it can melt during welding and cause serious damage to the equipment and even injure people nearby.
Welding Earth (Ground) Clamps: Why you will never get a good weld using a bad clamp
Conclusion
If you’re a welder, then you know that one of the most important things you need is a good clamp. But where does the work clamp actually attach? The answer is actually pretty simple – it attaches to the negative (-) side of the welding circuit.
This is because the current flows from the positive side to the negative side, and so the clamp needs to be attached to the negative side in order to complete the circuit. The work clamp also needs to be attached close to the welding area so that it can effectively ground the metal. If it’s not close enough, then there will be an arc between the electrode and the metal, which can cause problems.
So next time you’re setting up your welder, make sure that you attach the work clamp properly!