The ground clamp is one of the most important parts of a welding machine. It is responsible for providing a good electrical connection between the welder and the workpiece. There are many different types of ground clamps available on the market, but they all serve the same purpose.
The location of the ground clamp depends on the type of welding being performed.
In welding, the ground clamp is attached to the workpiece. This completes the circuit between the electrode and the workpiece, which allows current to flow. The ground clamp helps to ensure that there is a good connection between the electrode and the workpiece so that weld can be completed properly.
Ground Clamp in Welding
If you’re a welder, chances are you’ve used a ground clamp (or two) in your day. But what exactly is a ground clamp, and how does it work? Let’s take a look.
A ground clamp is a device that helps to ensure electrical safety when welding. It is attached to the welder’s electrode holder and then clamped onto the workpiece. This establishes an electrical connection between the welder and the workpiece, which helps to prevent arc flash and other hazards.
Ground clamps come in different sizes and styles, so it’s important to choose one that is compatible with your welding equipment and the type of weld you’re doing. Some ground clamps have built-in cables that connect directly to your power source, while others require separate cables. Make sure you have all the right supplies before starting your weld!
Once you have your ground clamp ready to go, simply attach it to the workpiece using either the jaws or magnets (depending on the style of clamp). Then turn on your power source and start welding! When you’re finished, be sure to disconnect the ground clamp before moving on to another task.
Welding can be dangerous if proper precautions aren’t taken. That’s why it’s important to always use a ground clamp when welding. By following these simple tips, you can help keep yourself safe while getting the job done right.
Welding Ground Positive Or Negative
Welding is a process of joining two materials, usually metals, by causing coalescence. This is done by heating the materials to their melting point and using a filler material to form a pool of molten metal that cools to create a permanent joint. Depending on the materials being joined and the welding process used, welding can be performed with or without adding pressure and/or using an electrode.
The most common types of welding are arc welding, oxy-fuel welding, resistance welding and laser beam welding. Each type uses different processes and techniques, but they all have one thing in common: they require an electrical current to create the arc that produces heat for welding. This electrical current can either be direct current (DC) or alternating current (AC).
DC is typically used for arc Welding because it provides a more stable arc than AC. However, AC can be used for certain types of Welding, such as mig Welding aluminum. The type of current you use will determine whether you weld with the ground electrode positive or negative.
If you’re using DC power, you’ll need to attach the ground clamp to the workpiece being welded. The ground electrode should be placed on the opposite side of where the arc will start. For example, if you’re right-handed and starting the arc at 12 o’clock, place the ground clamp at 6 o’clock.
This will ensure that any sparks created by the arc are directed away from you and allow for better control over the weld puddle. When using AC power, it doesn’t matter which side of the workpiece you attach the ground clamp to because sparks will alternate between sides as long as there’s clear metal behind where each spark occurs. However, it’s still recommended that you start at 12 o’clock so that sparks aren’t directed towards your face during Tig Welding aluminum Thin sheets Of sheet metal may need extra care when grounding them because they can conduct electricity too well; in this case use an old piece of scrap metal under your workpiece to help dissipate heat better .
What Happens If You Don’T Ground a Welder
If you don’t ground a welder, the electrical current will have nowhere to go but into the welder. This can cause serious damage to the welder and potentially start a fire. Always make sure to ground your welder before starting any welding projects.
Mig Welding Ground Positive Or Negative
When it comes to mig welding, there are two types of electrical current that can be used – direct current (DC) or alternating current (AC). Each type has its own advantages and disadvantages, so which one you use will depend on the particular application. In general, though, DC is typically used for mig welding.
There are two main reasons for this. First, DC provides a more stable arc than AC. This is important because it helps to ensure that the weld is of high quality.
Second, DC is less likely to cause metal spatter than AC. This means that there will be less of a mess to clean up after welding. If you’re not sure whether to use DC or AC for your mig welding project, it’s always best to consult with an experienced welder.
They’ll be able to advise you on the best course of action based on your specific needs.
How to Ground a Stick Welder
Most people don’t realize how important it is to ground a stick welder. If you don’t ground the welder properly, you run the risk of electrocuting yourself or starting a fire. In this blog post, we’ll show you how to properly ground a stick welder.
The first thing you need to do is find a good grounding point. This can be any metal that is in contact with the earth, such as a water pipe or metal fence post. Once you have found a good grounding point, attach the welding cable to it using an alligator clip or some other type of clamp.
Next, connect the other end of the welding cable to the negative (-) terminal on your welder. Make sure that the connection is secure and that there are no bare wires exposed. Now it’s time to weld!
When you’re finished welding, disconnect the negative terminal from your welder and then detach the cable from the grounding point. That’s all there is to it! By following these simple steps, you can help ensure your safety while using a stick welder.
Welding Ground Clamp Purpose
Welding is an important process in many industries, and a welding ground clamp is a vital part of the welding equipment. The purpose of the welding ground clamp is to provide a secure connection between the welder and the workpiece, which ensures a consistent flow of electricity during welding. Without a good grounding connection, welders can experience arcing and other problems that can cause serious injuries.
There are two main types of welding ground clamps: static and live. Static clamps are attached to the welder before starting the welding process, while live clamps are connected to the power source during welding. Live clamps are generally used for more difficult or dangerous welds, as they provide a more reliable connection.
Welding ground clamps must be made of high-quality materials in order to withstand the high temperatures and pressures involved in welding. The most common material for these clamps is copper, but other metals such as stainless steel or aluminum can also be used. It is important to choose a material that will not corrode under the harsh conditions created by welding.
When choosing a welding ground clamp, it is important to select one that is sized properly for the job at hand. Clamp sizes are determined by the diameter of the electrode being used. If you are using an electrode with a small diameter, you will need a small clamp; if you are using an electrode with a large diameter, you will need a large clamp.
Choosing the wrong size clamp can result in poor electrical contact and potentially dangerous consequences.
Stick Welding Ground Positive Or Negative
There are a few things to consider when deciding whether to ground your stick welding electrode positive or negative. Some factors include the type of metal you’re welding, the thickness of the metal, and your personal preference. If you’re welding steel, it’s generally recommended to ground the electrode positive.
This will help prevent oxidation of the weld area. For aluminum or stainless steel, grounding the electrode negative will help prevent contamination from oxide buildup. Thicker metals may require more heat to penetrate, so you may find that using a positive ground gives you better penetration.
If you’re welding two pieces of dissimilar metal together, it’s usually best to ground the electrode according to the piece that will be least affected by oxidation – so for steel and aluminum, that would be Aluminum (-), Steel (+). Ultimately, it comes down to experimentation and finding what works best for you on each individual project. There is no one right answer – so try out different techniques and see what works best for you!
Welding Ground Cable
Welding ground cables are an essential part of any welder’s toolkit. They are used to provide a safe and reliable connection between the welding machine and the workpiece, ensuring that any stray electricity is safely discharged. Ground cables come in a variety of sizes and lengths, so it’s important to choose the right one for your needs.
Here’s what you need to know about welding ground cables. The most important thing to look for in a welding ground cable is its amperage rating. This should be equal to or greater than the amperage rating of your welder.
The length of the cable also matters – longer cables will be more expensive, but they’ll also be more convenient as you won’t have to keep moving them around while you work. Finally, make sure that the connector on the end of the cable is compatible with your welder. When using a welding ground cable, always connect it directly to the workpiece – never connect it to another piece of metal such as a table or chair leg.
This could create a dangerous situation if electricity were to arc through the metalwork and into your body. Always disconnect the cable when you’re finished welding, and never leave it lying around where someone could accidentally step on it or trip over it. Welding ground cables are an essential part of any welder’s safety equipment.
Choose the right size and length for your needs, and take care when using them to avoid accidents.
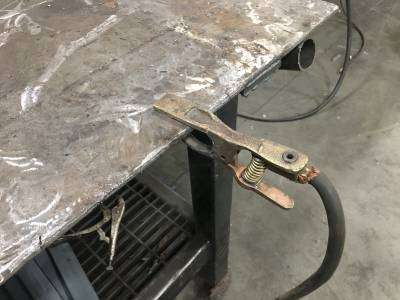
Credit: welderslab.com
Where is the Best Place to Attach the Ground Clamp?
There are a few different ways that you can go about attaching your ground clamp, and it really depends on what works best for you and your project. If you’re working with a small project, then attaching the ground clamp to a nearby piece of metal is usually sufficient. If you’re working with a larger project, then you may need to attach the ground clamp to a grounding rod driven into the earth.
Whichever method you choose, just be sure that the connection is secure and that there is good contact between the metal and the clamp.
What Will Happen If the Ground Clamp is Not Placed Correctly?
If the ground clamp is not placed correctly, it could result in an electrical hazard. The ground clamp is used to create a safe and secure connection between the electrical system and the grounding rod. If the ground clamp is not properly secured, it could allow electricity to flow through the grounding rod and into the earth, which could pose a serious safety risk.
What is a Ground Clamp in Welding?
A ground clamp is an essential piece of equipment for any welder. It is used to create a secure connection between the welding machine and the workpiece, ensuring that the electrical current stays where it should. Ground clamps come in a variety of sizes and styles, so it is important to choose one that is compatible with your welding machine and the type of welding you will be doing.
Can You Hold the Ground Clamp When Welding?
It is common for people to ask whether or not they can hold the ground clamp when welding. The answer is that it depends on the type of welding you are doing. If you are using a standard arc welder, then it is generally safe to hold the ground clamp in your hand.
However, if you are using a more powerful welder such as a MIG welder, then it is not advisable to hold the ground clamp in your hand as this could result in serious injury.
Welding Earth (Ground) Clamps: Why you will never get a good weld using a bad clamp
Conclusion
When welding, it’s important to know where the ground clamp goes. The ground clamp needs to be attached to a metal surface that is in contact with the earth. This will help ensure that any sparks or heat from the welding process are properly grounded and won’t cause any damage or injury.