welding aluminum is not as difficult as it may seem at first glance. In fact, with the right tools and a little practice, anyone can weld aluminum with great results. The most important thing to remember when welding aluminum is to use the correct tools and techniques.
First, you will need an aluminum welding machine. This type of welder uses high frequency waves to create an electrical arc between the electrode and the metal being welded. The arc melts the metal, which allows it to be fused together.
There are many different types of aluminum welding machines on the market, so it is important to do your research and choose one that will work best for your needs.
Next, you will need a wire feeder. This device feeds a thin wire through the welding machine and into the area being welded.
The wire provides filler material for the weld and helps to create a strong bond between the two pieces of metal.
Finally, you will need some basic safety equipment such as gloves, a mask, and eye protection. Welding can be dangerous if proper precautions are not taken.
Always follow all safety instructions that come with your welding machine and wear protective gear when operating it.
When welding aluminum, there are a few tools that are needed in order to get the job done right. First, you will need an electrode holder and lead assembly that is rated for use with aluminum. Next, you will need a power source that can provide the correct amperage for welding aluminum.
Finally, you will need a wire feeder if you are using a MIG welder.
With these three things, you should be able to weld aluminum without any issues. Of course, there are other things that can make your life easier when welding aluminum such as gloves, a face shield, and proper ventilation.
But those three things are the bare minimum that you need in order to start welding aluminum.
Mig Welding Aluminum
Mig Welding Aluminum
Mig welding aluminum is a process that uses an electrode to create an electric arc between the metal and the wire. The heat from the arc melts the aluminum, which is then welded to the base metal.
There are several benefits to mig welding aluminum. First, it is a relatively fast process. Second, it produces less fumes than other welding processes.
Third, it is easier to control the heat of the arc, making it possible to produce high-quality welds. Finally, mig welding aluminum produces less spatter than other processes, making cleanup easier.
Despite these advantages, there are some challenges associated with mig welding aluminum.
First, it can be difficult to establish and maintain an arc due to the low conductivity of aluminum. Second, aluminum oxide must be removed from the surface before welding can begin, and this can be challenging in windy conditions. Third, because aluminum has a lower melting point than steel, it is important to use lower temperatures when welding to avoid warping or damaging the metal.
Joining Aluminium Without Welding
Joining aluminium without welding is a process that can be used to create strong and reliable joints between pieces of aluminium without the need for heat or welding. This method is often used when joining aluminium to other metals, as it avoids the potential for damage to the metal from heat or sparks.
There are several methods that can be used to join aluminium without welding, but the most common is known as mechanical fastening.
This involves using screws, bolts, or rivets to hold the two pieces of metal together. Mechanical fasteners can be made from a variety of materials, including steel, brass, or even titanium.
Another method of joining aluminium without welding is known as adhesive bonding.
This involves using an adhesive material to bond the two pieces of metal together. Adhesive bonding can be done with a variety of different adhesives, including epoxy resins and cyanoacrylate glues.
Both mechanical fastening and adhesive bonding are effective methods for joining aluminium without welding.
However, it is important to note that these methods should only be used on small projects where the joint will not be subject to high stresses. For larger projects or joints that will be under high stress, welded joints are still considered the best option.
What Do You Need to Weld Aluminum
If you’re planning on welding aluminum, there are a few things you’ll need to have on hand first. Here’s a quick list of what you’ll need to get started:
-An AC welder that is specifically designed for welding aluminum.
You can’t use a standard AC arc welder for this – the results won’t be pretty.
-Aluminum welding wire. This can be found at most hardware stores or online.
Make sure you get the right gauge and type of wire for your project.
-A face mask and gloves. Welding aluminum produces harmful fumes, so it’s important to protect yourself while you work.
With these supplies in hand, you’re ready to start welding! Just remember to take your time and practice on some scrap pieces before tackling your final project.
How to Weld Aluminum With a Stick Welder
If you’re looking to weld aluminum with a stick welder, there are a few things you need to know. First, it’s important to use an electrode that is specifically designed for welding aluminum. Second, you need to make sure the metal is clean before beginning to weld.
Third, when welding aluminum it’s important to use lower amperage than you would when welding other metals.
Welding Aluminum
If you’re planning on welding aluminum, there are a few things you should know first. Aluminum is a difficult metal to weld because it’s highly reactive. That means it easily oxidizes, which can lead to welding problems.
To avoid those issues, make sure you use the right welding technique and tools. You also need to be extra careful when preparing your materials for welding. If everything is done correctly, though, you’ll be able to weld aluminum like a pro!
Tig Welding Aluminum
Tig Welding Aluminum is a process that uses a non-consumable tungsten electrode in order to produce an arc. This arc is then used to heat up and melt the aluminum in order to weld it. Tig Welding Aluminum can be used on both thin and thick materials, making it a versatile welding method.
In addition, Tig Welding Aluminum produces little smoke and spatter, making it a cleaner option than other welding methods.
Cheapest Way to Weld Aluminum
Welding aluminum is a great way to save money and time when joining two pieces of metal together. There are several ways to weld aluminum, but the cheapest and most effective method is through the use of an oxy-acetylene torch. This type of torch is easy to use and produce a strong weld that will hold up under stress.
The key to success when welding aluminum is to practice on some scrap pieces first so that you get a feel for the process. Here are some tips on how to weld aluminum using an oxy-acetylene torch:
1) Clean the area where you will be welding with a wire brush.
This will remove any dirt or debris that could prevent a good weld from forming.
2) Set up your oxy-acetylene torch according to the manufacturer’s instructions. Make sure that you have a good flame before starting to weld.
3) Hold the torch at a 45 degree angle and start the welding process by melting the edge of one piece of metal. Then, touch the tip of the other piece of metal to the molten pool and continue welding around the entire joint.
4) Allow the welded joint to cool before handling it or putting any stress on it.
Can You Weld Aluminum to Steel
Welding aluminum to steel is possible, but it is not recommended because of the high risk of cracking and corrosion. The best way to weld aluminum to steel is by using an aluminum welding rod with a low melting point. This will help to prevent the formation of cracks and corrosion.
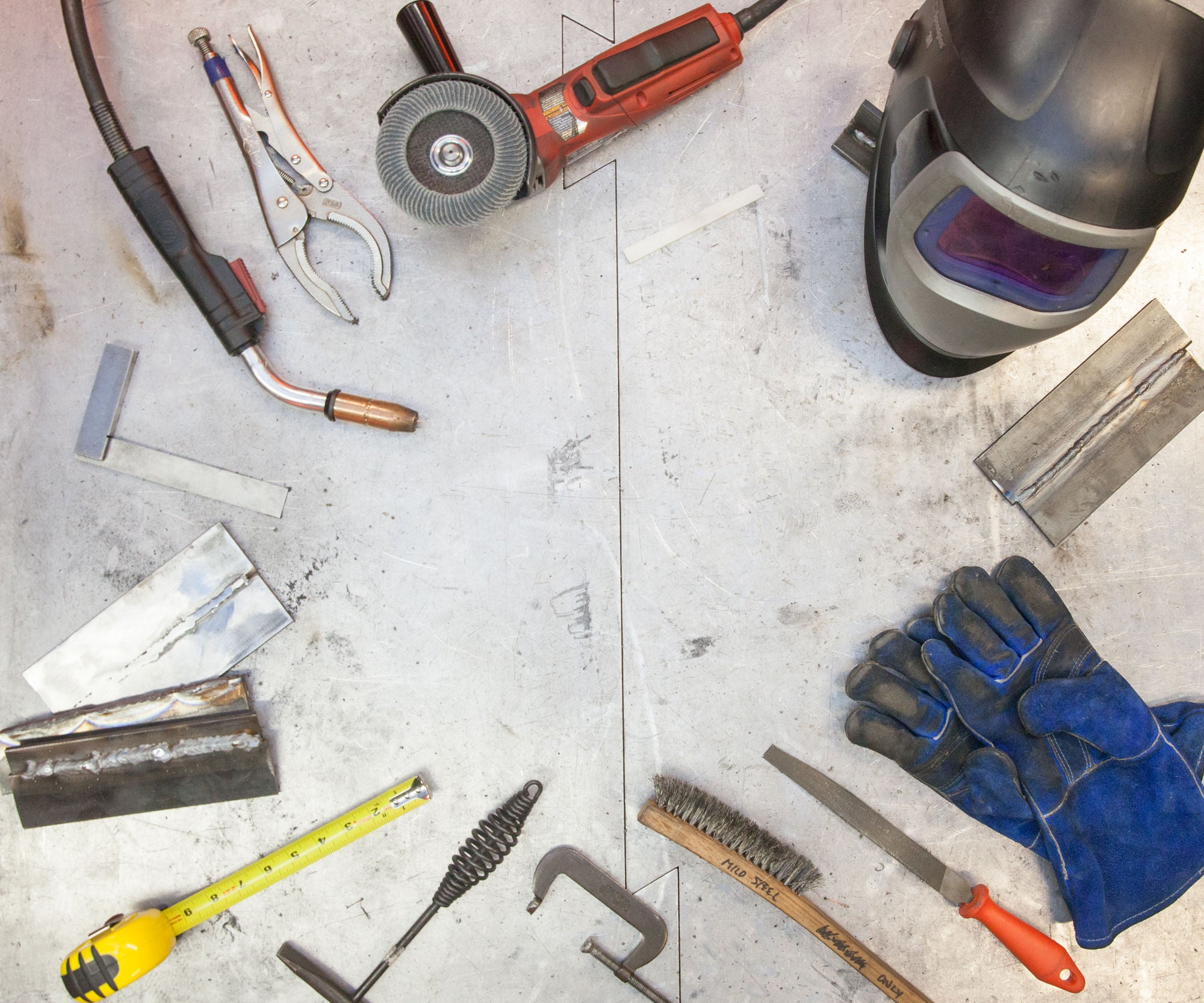
Credit: www.instructables.com
What is the Most Common Way to Weld Aluminum?
There are a few different ways to weld aluminum, but the most common method is TIG welding. TIG stands for “tungsten inert gas” and uses a non-consumable tungsten electrode to create an arc between the metal being welded and the welding torch. This arc is then used to heat up the metal, which melts and fuses the two pieces together.
TIG welding is preferred for aluminum because it produces a cleaner weld than other methods like MIG welding or stick welding. It also doesn’t require any filler material, so you can get a strong join without having to add anything extra. However, TIG welding can be tricky to learn and takes some practice to master.
But once you get the hang of it, it’s a great way to weld aluminum!
Can You Weld Aluminum With a Regular Mig Welder?
Yes, you can weld aluminum with a regular MIG welder. However, there are a few things you need to keep in mind. First, you need to use a wire that is specifically designed for welding aluminum.
Second, you need to use an argon gas mixture when welding aluminum. Third, the welding speed for aluminum should be slower than the speed used for steel. Finally, it is important to clean the aluminum before welding it.
What is Best for Welding Aluminum?
There are a few different ways to weld aluminum, but the two most common are TIG and MIG welding. TIG welding is typically the best option for welding aluminum, as it produces a cleaner weld than MIG welding and is less likely to cause warping or other damage to the metal. However, MIG welding can be used for aluminum if necessary, and some people prefer it because it is easier to learn than TIG welding.
Do You Need an Aluminum Welder to Weld Aluminum?
Assuming you are asking if aluminum can be welded with a standard welding machine, the answer is yes. Aluminum can be welded with any type of welder, but it is important to use the correct type of wire and gas. When welding aluminum, it is important to use an Argon gas mixture.
This is because Argon prevents oxygen from getting into the weld and causing it to oxidize. It is also important to use a wire that has a higher level of silicon. This helps to prevent hot cracking, which can be a problem when welding aluminum.
How to "Weld" Aluminum for Beginners
Conclusion
Welding aluminum is a process that requires the use of specialized equipment and techniques. In order to weld aluminum properly, you will need a power source, filler material, and shielding gas. You will also need to use different welding methods and parameters than you would when welding other materials.