There are many different types of welding systems on the market today. Gas metal arc welding, or GMAW, is one of the most popular. A GMAW system typically includes a power source, wire feeder, and gas tank.
The power source provides the energy needed to create an arc between the electrode and the workpiece. The wire feeder feeds filler metal into the arc. The gas tank supplies shielding gas to protect the weld from contamination.
When it comes to welding, there are many different types of systems that can be used. However, most systems have certain components that are essential for the process. For example, a gas metal arc welding (GMAW) system typically contains the following components:
-A power supply: This provides the electricity needed to create the arc between the electrode and the workpiece.
-An electrode holder: This holds the electrode in place and is connected to the power supply.
-An electrode: This is made of a conductive material and is used to create the arc.
It is consumable, meaning it will need to be replaced periodically.
-A gas tank: This contains shielding gas, which helps protect the weld area from contamination.
Describe the Spot Welding Process Using a Gma Welder.
Spot welding is a process in which two pieces of metal are joined together by heating them with an electric arc. The heat from the arc melts the metal and creates a weld bead that holds the two pieces together. Spot welding is commonly used to join sheet metal and thin-walled tubing.
The spot welding process is relatively simple. First, the two pieces of metal to be welded are placed together so that they touch at the spot where the weld will be made. Then, an electrode is placed on each side of the joint and an electric current is passed through the electrodes.
The current causes an arc to form between the electrodes, which heats the metals and creates a weld bead.
There are several factors that must be considered when spot welding, such as electrode size and type, amperage, voltage, and travel speed. By carefully controlling these factors, it’s possible to create strong welds that will hold up under stress.
How is the Wire-Feed Speed Changed With a Linear Feed System?
The wire-feed speed is changed with a linear feed system by altering the voltage that is supplied to the system. By increasing or decreasing the voltage, the wire-feed speed can be increased or decreased. This allows for greater control over the welding process and helps to ensure that the welds are of high quality.
What Factors Must Be Considered When Selecting Which Mode of Metal Transfer to Use?
The mode of metal transfer is an important process parameter in gas metal arc welding (GMAW) that can have a significant effect on weld bead shape, penetration, and other weld characteristics. When selecting the most appropriate mode of transfer for a given application, a number of factors must be considered, including:
-Welding current and voltage
-Wire feed speed
-Gas type and flow rate
-Polarity
With regard to welding current and voltage, the three main modes of metal transfer in GMAW are short circuit transfer, globular transfer, and spray transfer. Short circuit transfer is the most common mode used in GMAW and is characterized by low welding currents (usually below 100 A) and voltages (typically between 15 and 20 V). This results in small droplets being transferred across the arc gap with very little spatter.
Globular transfer is achieved at slightly higher currents and voltages than short circuit transfer; as such, larger droplets are transferred across the arc gap along with increased spatter. Spray transfer occurs at still higher currents and voltages (>100 A & >20 V), resulting in a stream of molten metal being sprayed across the arc gap. This mode offers high deposition rates but also produces considerable spatter.
The wire feed speed is another important process parameter that must be considered when selecting the most appropriate mode of metal transfer. In general, increasing the wire feed speed will result in an increase in the size of droplets being transferred across the arc gap. As such, slower wire feed speeds are typically used for short circuit transfers while faster wire feed speeds are more commonly used for globular or spray transfers.
The gas type and flow rate play a critical role in determining which mode of metaltransfer will be most successful. For instance, using an argon/CO2 shielding gas mix will generally promote globular or spray transfers whereas using 100% CO2 will tend to promote short circuit transfers. The flow rate of shielding gas is also important; too high of a flow rate can actually hinder certain modes oftransfer by causing instability within the arc column.
Finally, polarity must be considered when selecting which modeofmetaltransfer to use. Direct current electrode negative (DCEN) electrodepositive(DCEP) tends to produce shorter arcs with less sputter than reversepolarity(DCRP).
Where is the Drive Motor Located in a Pull-Type Wire-Feed System?
In a pull-type wire-feed system, the drive motor is located on the spool of welding wire. This allows the motor to constantly feed wire through the torch, keeping a steady supply of welding material available. The location of the drive motor also makes it easy to change out spools of welding wire when necessary.
Describe the Weld Produced by a Forehand Welding Angle.
When welding, the angle at which you hold the torch can have a big impact on the quality of the weld. A forehand welding angle is created when you hold the torch at an angle that points toward the direction of travel. This type of weld is often used for repairing metal objects or for joining two pieces of metal together.
There are several benefits to using a forehand welding angle. First, it allows you to see what you’re doing more clearly than if you were holding the torch in another position. Second, it gives you more control over the weld bead, making it easier to produce a high-quality weld.
Finally, this position puts less stress on your body and arms, making it easier to weld for extended periods of time.
If you’re new to welding or are looking for ways to improve your welding technique, give forehand welding a try!
Describe the Current Produced by the Pulsed-Arc Metal Transfer Mode
The pulsed-arc metal transfer mode is a process that uses an electric arc to weld two pieces of metal together. The arc is produced by an electrode that is connected to a power source and then pulsed on and off. The heat from the arc melts the metal, which allows the two pieces to be joined together.
This welding process is often used for joining thin sheets of metal together, such as in the automotive industry. It can also be used for thicker materials, but it may not be as effective as other welding processes for those applications.
Describe the Globular Transfer Process
The globular transfer process is a way to move large amounts of data between two devices without using an intermediary. This can be done by physically connecting the two devices with a cable, or by using a wireless connection.
In order to transfer data using the globular transfer process, both devices must be connected to the same network.Once they are connected, one device will initiate the transfer by sending a request to the other device. The receiving device will then confirm that it is ready to receive the data. Once the receiving device is ready, the sending device will begin transferring the data.
The amount of time that this takes will depend on the size of the data being transferred. Once the data has been transferred, both devices will disconnect from each other and return to their normal state.
Mig Welding Machine Parts And Function
Mig welding machines are used to weld various metals together. There are several parts to a mig welding machine, which include the power supply, wire feeder, and torch. The power supply provides the electricity needed to heat up the metal so that it can be joined together.
The wire feeder feeds the wire into the torch, which then melts the metal and joins it together.
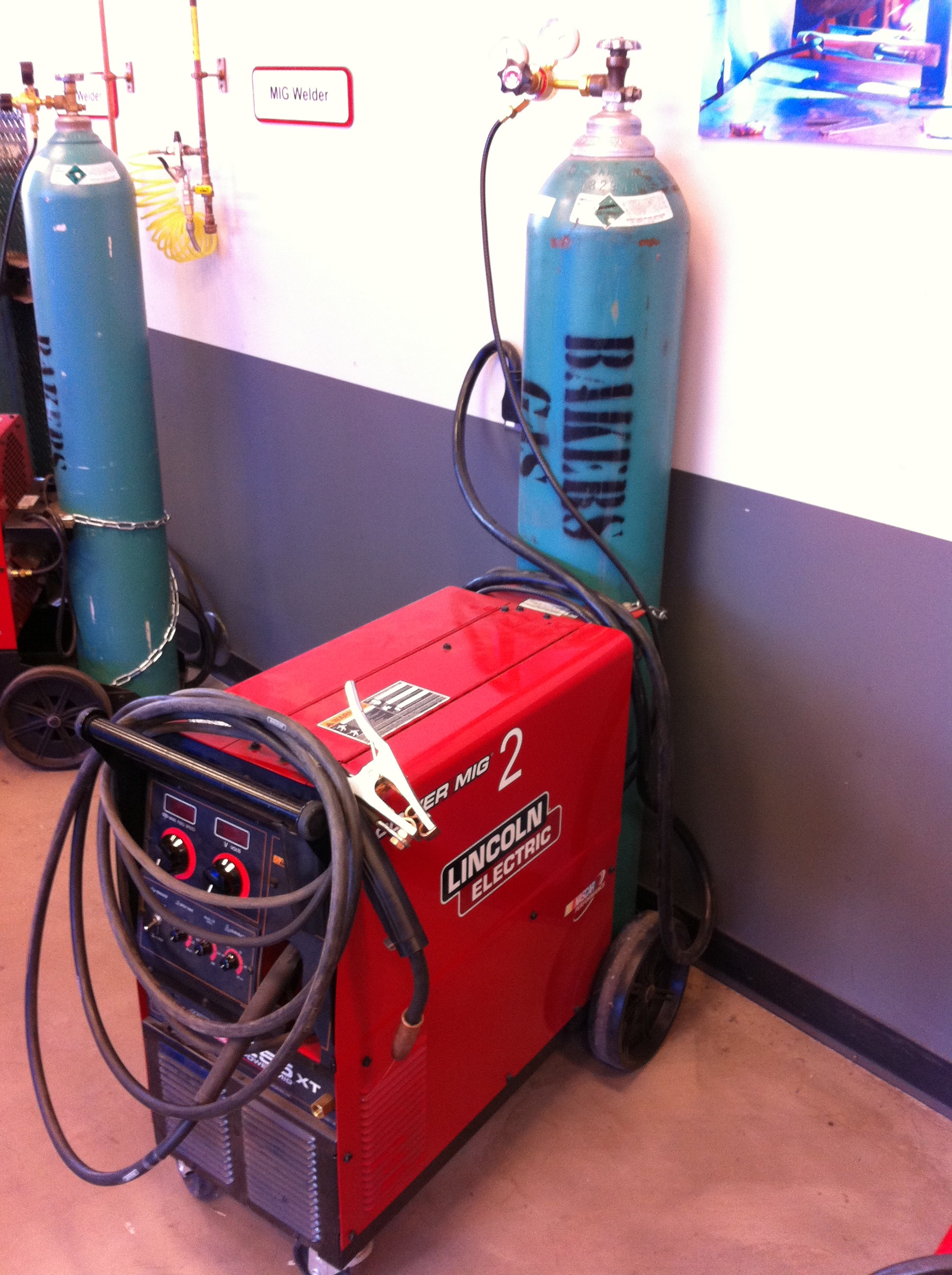
Credit: www.instructables.com
What are the Basic Components of a Gmaw Welding Station?
In a gas metal arc welding (GMAW) station, there are several key components that work together to create the weld. The first is the power source, which provides the electricity needed to create the arc. This can be either AC or DC, and the type of power source you use will determine the other components you need in your station.
For example, if you’re using an AC power source, you’ll need an AC welder.
Next is the welding torch, which is used to direct the arc and focus the heat on the area being welded. The torch also has a gas valve that controls the flow of shielding gas around the arc.
This gas protects the weld from contamination and helps to create a strong bond between metals.
Last but not least is filler metal, which is used to join two pieces of metal together. Filler metal comes in many different forms, including rods, wires and even pellets.
When choosing filler metal for your GMAW station, it’s important to consider factors such as compatibility with your base metals and desired strength of your finished weld.
What are the 4 Major Components of a Gmaw Setup?
In order to set up a GMAW welding machine, there are four major components that must be put in place. These are the power supply, gas cylinder, electrode holder, and ground clamp. Each of these pieces plays an important role in the welding process and must be set up correctly in order for the machine to function properly.
The power supply is responsible for providing the electrical current that is needed to create the arc between the electrode and the work piece. This current can either be AC or DC, but most modern machines use DC because it provides a more stable arc. The power supply also has controls that allow the welder to adjust the amperage and voltage output, which will determine how hot the arc is and how fast the metal melts.
The gas cylinder contains shielding gas that helps to protect the weld area from contamination. This gas typically consists of argon or carbon dioxide, and sometimes a mix of both. The amount of gas flow will need to be adjusted based on what type of metal is being welded and what kind of joint is being made.
Too much or too little gas can result in poor quality welds, so it’s important to get this setting right.
The holder should be firmly attached to avoid any movement during welding which could cause problems with maintaining a consistent arc length. Finally, the ground clamp needs to be attached to something metal near where you’ll be welding. This provides a path for electricity to flow back into the machine after passing through your work piece (and ultimately prevents you from being electrocuted).
Make sure that this clamp is snug against whatever you’re attaching it too so that there’s good electrical contact. Once everything is hooked up correctly, you’re ready to start welding!
What Parts of a Typical Gma Welding Gun Can Be Replaced?
Welding guns are made up of several different parts, all of which can be replaced if necessary. The most common parts that need to be replaced are the contact tip, nozzle, and diffuser. The contact tip is the part of the gun that actually touches the welding wire and conducts the electrical current.
Over time, these tips can become worn or damaged and will need to be replaced. Nozzles are responsible for directing the flow of gas from the welder to the weld joint. Diffusers help to evenly distribute the gas around the welding joint.
What Type of Welding is Gma Welding?
GMA welding, also known as gas metal arc welding, is a type of welding that uses an electric arc to weld metals together. The metal that is being welded is melted by the heat of the electric arc and forms a pool of molten metal called a weld pool. This weld pool can be used to join two pieces of metal together or to fill in any gaps in the metal.
GMA welding is a very versatile type of welding and can be used on many different types of metals. It is often used to weld aluminum, stainless steel, and other non-ferrous metals. GMA welding can be done with or without filler material, and it can be done in all positions (including vertical and overhead).
One advantage of GMA welding over other types of welding is that it produces less fumes and smoke. This makes it ideal for use in confined spaces or areas where there is poor ventilation. Additionally, GMA Welding is generally considered to be a safer process than other types of welding because it does not produce ultraviolet light or radiation.
What is MIG Welding? (GMAW)
Conclusion
The gas metal arc welding (GMAW) process uses an electric arc to weld metals. This process is also known as metal inert gas (MIG) welding. GMAW is a popular welding method because it is relatively easy to learn and can be used on a variety of materials, including aluminum, stainless steel, and mild steel.
GMAW systems consist of four main components: the power source, the wire feeder, the gas supply, and the torch. The power source provides the electricity needed to create the arc. The wire feeder feeds the wire into the arc.
The gas supply provides shielding gas to protect the weld from contamination. The torch holds the electrode and directs the arc onto the workpiece.