Most air compressors are single stage, meaning they have one cylinder that compresses the air. A two stage air compressor has two cylinders, with the first one drawing in air and compressing it to a lower pressure than a single stage compressor. The second cylinder then takes the low-pressure air from the first and further compresses it to an even higher pressure.
Two stage compressors are more expensive than single stage compressors, but they’re also more efficient.
- 1) Disconnect the power supply to your air compressor
- 2) Locate the pressure switch on your air compressor
- The pressure switch will have two sets of wires running to it, one from the power supply and one from the motor
- 3) Using a wrench or pliers, loosen the terminal screws on the pressure switch and remove the wires
- 4) Connect one set of wires to each side of the new pressure switch
- Make sure to connect the correct wire to each side, as reversing them will cause your air compressor to not function properly
- 5) Tighten down the terminal screws and reattach any covers that may be present on your pressure switch
- 6) Reconnect your power supply and turn on your air compressor
How to Wire a 5 Hp Air Compressor
If you’re looking to wire a 5 hp air compressor, there are a few things you need to know first. For one, you need to make sure that the voltage and amperage requirements of the compressor are compatible with your power source. Additionally, it’s important to choose the right size wire for your application.
Here’s a step-by-step guide on how to wire a 5 hp air compressor:
1. Start by shutting off all power to the area where you’ll be working. This includes both the main power supply and any backup generators.
2. Next, remove the cover from the junction box on the air compressor. Inside, you should see three terminals labeled “L1,” “L2,” and “T1.”
4. Once you’ve confirmed that there is no power present, begin connecting your wires. The black (or hot) wire should be attached to terminal “L1.” The white (neutral) wire should be attached to terminal “L2.”
Finally, attach the green (or ground) wire to terminal “T1.” 5. Once all of your wires are securely connected, replace the cover on the junction box and turn on all power sources in the area. Your air compressor should now be operational!
30 Amp Air Compressor Plug
An air compressor is a device that uses an electric motor to power a piston that compresses air. The compressed air is then used to power tools such as drills, nail guns, and impact wrenches. A 30 amp air compressor plug is a type of plug that is typically used to connect an air compressor to an electrical outlet.
The 30 amp air compressor plug is designed for use with compressors that have a maximum draw of 30 amps. This type of plug offers a higher amperage than a standard 15 amp plug, which means it can handle more powerful compressors. In addition, the 30 amp air compressor plug has a thicker wire gauge than a standard 15 amp plug, which makes it better suited for high-power compressors.
When shopping for a new air compressor, be sure to check the amperage rating of the unit and compare it to the ratings of different types of plugs. If you have any questions about which type of plug is right for your needs, consult with an electrician or other qualified professional.
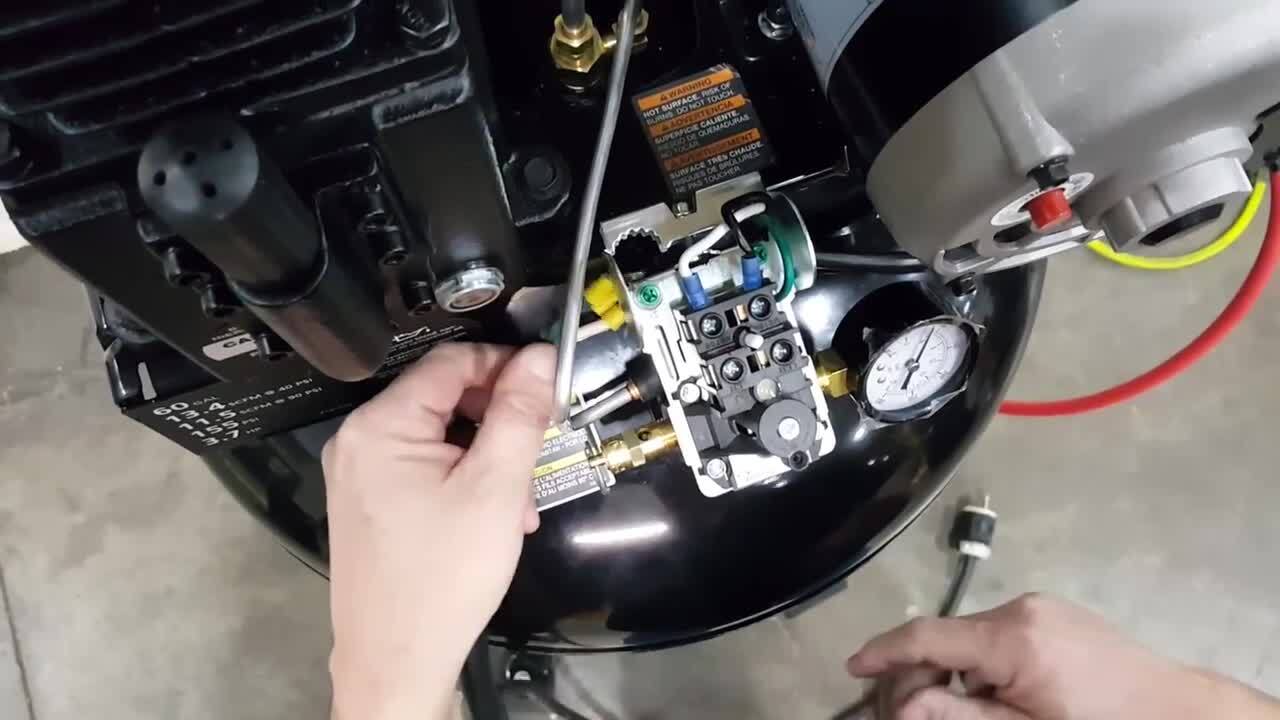
Credit: www.homedepot.com
How Do 2 Stage Air Compressors Work?
Two stage air compressors are designed to deliver more consistent pressure than their single stage counterparts. They do this by compressing the air in two steps, rather than just one. In the first stage, a smaller piston delivers a low-pressure blast of air into the second stage.
This second stage is where the actual compression takes place. The air is compressed by a larger piston, and then delivered to your desired destination – whether that’s an air tool, or a storage tank.
This makes them ideal for applications where sustained high pressure is required – such as automotive work, or running pneumatic tools all day long.
What Size Breaker Do I Need for a 240V Air Compressor?
If you’re asking yourself what size breaker do I need for a 240v air compressor, the answer is most likely a 60-amp double-pole breaker. However, it’s important to consult your air compressor’s owner’s manual to be absolutely sure – some models may require a different size.
As far as installation goes, if you’re not comfortable working with electrical circuits, it’s always best to hire a professional electrician.
But if you are confident in your abilities, installing a 240v air compressor circuit is relatively straightforward.
First, shut off power at the main panel and remove the covers. Next, connect the black (hot) wires to the brass terminals on the breaker, and connect the white (neutral) wires to the silver terminals.
Finally, screw on the covers and restore power at the main panel.
Once again, though, make sure to check your owner’s manual for specific instructions regarding wiring and breakers – following these general steps should get you close, but every model is different. And when in doubt, err on the side of caution and call a professional electrician.
Does 220 Air Compressor Need Neutral?
No, 220 air compressors do not need a neutral wire. The 220 voltage is single phase and the air compressor will work without a neutral wire.
What is the Advantage of a 2 Stage Compressor?
If you’re looking for an air compressor that can handle high-pressure applications, then a two-stage air compressor is the way to go. Here are some of the advantages of using a two-stage air compressor:
1. Two-stage compressors can reach higher pressures than single-stage compressors.
This is because they have two cylinders, with the first cylinder compressing the air to a lower pressure before it moves on to the second cylinder where it’s compressed to an even higher pressure. This means that two-stage compressors are ideal for applications that require high pressures, such as painting or sandblasting.
2. Two-stage compressors are more efficient than single-stage compressors.
This is because they don’t have to work as hard to reach high pressures since they have two cylinders working together. As a result, two-stage compressors use less energy and run cooler than single-stage compressors, which makes them more durable in the long run.
3. Two-stage compressors are quieter than single-stage compressors.
This is because they have slower RPMs (revolutions per minute), which creates less noise overall. If you’re looking for an air compressor that won’t disturb your neighbours or cause too much noise in your own home, then a two-state compressor is a good option.
Quincy QT-54 single phase 220v 2-stage air compressor installation (DIY style)
Conclusion
If you’re looking to wire a 2 stage air compressor, there are a few things you need to know. First, make sure that the power is off and disconnect the air lines from the unit. Next, remove the access panel and locate the pressure switch.
Once you’ve found the pressure switch, disconnect the wires from it. Now, take your new 2 stage air compressor pressure switch and connect it to the wires coming from your power source. Finally, reattach the access panel and turn on the power.