In order to weld tool steel to mild steel, one must first understand the difference between the two types of steel. Tool steel is a type of carbon steel that is known for its hardness and resistance to wear. Mild steel, on the other hand, is a type of low carbon steel that is much easier to weld.
When welding these two types of steel together, it is important to use a filler material that will not cause the tool steel to become harder. In addition, the welder must be sure to use enough heat when welding so that the tool steel does not crack.
- Choose the right welding process for your application
- If you are welding tool steel to mild steel, you will need to use a process that is compatible with both materials
- Clean the surfaces of the tool steel and mild steel before welding
- This will help ensure a strong bond between the two materials
- Set up your welding equipment according to the chosen welding process
- Begin welding the tool steel to the mild steel, using slow and steady strokes
- Keep the weld area clean and free of debris while you work
- Finish welding and allow the joint to cool before handling it further
Welding Tool Steel With 7018
Welding tool steel with 7018 is a great way to get a strong, durable weld. This type of steel is known for its resistance to wear and tear, making it ideal for tools that will see a lot of use. 7018 is also easy to work with, making it a good choice for welding projects where precision is important.
Here are some tips on how to get the best results when welding tool steel with 7018.
Before you begin welding, make sure that your tools and materials are in good condition. If you’re using old or damaged equipment, it’s more likely that your welds will be weak or prone to breaking.
Always check your torch and electrodes for damage before beginning any welding project.
It’s also important to choose the right filler rod for your project. When welding tool steel, 7018 rods are generally the best choice as they provide high levels of strength and durability.
However, if you’re working on a smaller project or one that doesn’t require as much strength, another type of filler rod may be more suitable. Be sure to consult with an expert before choosing the right filler rod for your project.
When you’re ready to start welding, always make sure that your area is well-ventilated.
Welding produces harmful fumes that can be dangerous if inhaled in large quantities.
Tool Steel Filler Rod
Tool steel is a type of carbon steel that is specially designed for manufacturing tools. It is hard and durable, making it ideal for creating cutting and shaping tools. Tool steel generally has a higher carbon content than regular carbon steel, which gives it the strength and hardness required for tool-making.
There are different types of tool steel, each with its own properties and applications.
Some common types of tool steel include: high-speed steel (HSS), cold-work steel, hot-work steel, and shock-resistant steel. HSS is the most widely used type of tool steel because it can be used to create a wide range of tools, including drill bits, saw blades, and end mills.
Cold-work steels are designed for use in low-temperature applications where high levels of wear resistance are needed. Hot-work steels are ideal for applications where high temperatures are involved, such as forging or casting metals. Shock-resistant steels are designed to resist impact and shock loading, making them ideal for use in hammers and other hand tools.
When choosing a tool steel filler rod, it’s important to consider the specific application the rod will be used for. The type of metal being welded also plays a role in selecting the right filler rod; HSS rods are typically used on stainless steels and cast irons while cold-work rods are better suited for welding low alloy or carbon steels. Once the application and metal have been determined, you can then select a rod with the appropriate chemistry and mechanical properties.
Welding D2 Tool Steel
D2 tool steel is a high-carbon, high-chromium alloy that is known for its excellent abrasion and wear resistance. It is often used in cutting and forming tools, as well as in dies and punches. In order to weld D2 tool steel, it is important to use the proper welding techniques and equipment.
D2 tool steel has a carbon content of 1.5-1.7%, which makes it a very hard material. It also has a chromium content of 11-13%. This combination of elements gives D2 tool steel its excellent wear resistance properties.
However, these same characteristics make D2 tool steel difficult to weld. In order to weld D2 tool steel successfully, it is important to use the proper welding techniques and equipment.
One common method for welding D2 tool steel is gas tungsten arc welding (GTAW).
GTAW uses a nonconsumable tungsten electrode to produce the arc between the workpiece and electrode. The arc heats the workpiece material, causing it to melt and flow around the electrode. GTAW is typically used for thin workpieces or for applications where precise control of heat input is necessary.
Another popular method for welding D2 tool steel is gas metal arc welding (GMAW). GMAW uses a consumable wire electrode that melts and becomes part of the weld pool along with the base metal. The GMAW process can be performed in either short circuit mode or spray transfer mode.
Short circuit mode produces smaller droplets that are less likely to cause excessive heat input into the base metal. Spray transfer mode produces larger droplets that provide more heat input but can result in porosity if not properly controlled.
Welding M4 Tool Steel
Welding M4 Tool Steel
M4 tool steel is a high speed steel that is often used in cutting tools. It is extremely hard and durable, making it an ideal choice for welding projects.
However, because of its hardness, it can be difficult to weld without the proper tools and techniques. In this blog post, we’ll discuss the best ways to weld M4 tool steel so that you can complete your project with ease.
Before beginning any welding project, it’s important to have the right tools on hand.
For M4 tool steel, you’ll need a TIG welder with argon gas and tungsten electrodes. You should also have a face mask and gloves to protect yourself from the heat and sparks. Once you have your equipment ready, you can begin preparing your workspace.
When welding M4 tool steel, it’s important to create a strong joint between the two pieces of metal. This can be achieved by using a TIG welder with argon gas as your shielding agent. When welding, start at the center of the joint and work your way outwards in small circles until you reach the edge of each piece of metal.
As you weld, keep the torch at a 45 degree angle so that the heat is evenly distributed across the joint.
Once you’ve completed welding around the entire joint, allow it to cool before removing the mask or gloves. Inspect your work to make sure that there are no weak spots or gaps in the welded area.
If everything looks good, congratulations – you’ve successfully welded M4 tool steel!
Welding D2 to Mild Steel
Welding D2 to Mild Steel
D2 is an air hardening, high carbon, high chromium tool steel. It has excellent abrasion resistance and toughness properties.
D2 also has a very high resistance to wear. In order to weld D2 to mild steel, the following parameters must be observed:
-Preheat temperature: 400-500°F
-Interpass temperature: 500-600°F
-Postweld heat treatment: Tempering at 1050-1150°F for 1 hour followed by air cooling
The above are only guidelines and should be adjusted according to the specific application.
Welding S5 Tool Steel
Welding S5 tool steel is a process that can be used to join two pieces of this material together. This alloy is known for its high hardness and wear resistance, making it a popular choice for many applications. In order to weld S5 tool steel, you will need to use an arc welding process.
This means that you will need to have access to an electric power source and the necessary equipment. The most common type of arc welding process used for this material is gas tungsten arc welding (GTAW).
S5 tool steel has a carbon content between 0.45-0.55%.
It also contains other alloying elements such as chromium, molybdenum, vanadium, and tungsten. The combination of these elements give the alloy its high hardness and wear resistance properties. In order to weld S5 tool steel successfully, you must use a filler material that contains at least 25% chromium.
One challenge that you may face when welding this material is its high hardness. This can make it difficult to create a strong weld joint if the correct precautions are not taken. One way to overcome this challenge is by using what is known as a “pre-heat” technique.
This involves heating up the area around the weld joint before beginning the actual welding process. By doing this, you can help reduce the risk of cracking or other problems with your weld joint.
Weld Mold 958 Alternative
Weld Mold 958 is a nickel-based alloy designed for welding austenitic stainless steels of similar composition in the annealed or tempered condition. It can also be used for joining austenitic to ferritic stainless steels. Weld Mold 958 is covered by AWS A5.11/A5.11M and ASME SFA 5.11/SFA 5.11M Specifications and is available as bare electrode wire and covered electrode.
Possible Alternatives
Although Weld Mold 958 is a great option for welding austenitic stainless steel, there may be some cases where an alternative weld metal might be a better fit.Some possible alternatives to Weld Mold 958 include:
– ER 309L: For welding 304 or 316 base metals
– E NiCrFe-7: For welding Hastelloy C276
Welding W1 Tool Steel
Welding W1 tool steel can be a challenge, but with the right tools and techniques it can be done successfully. Here are some tips for welding W1 tool steel:
– Use a low amperage setting on your welder.
Too much heat will cause the steel to warp.
– Preheat the steel before welding. This will help prevent warping and cracking.
– Use a welding rod that is compatible with W1 tool steel. Incompatible rods can cause the weld to crack.
– Use plenty of flux when welding.
This will help protect the weld from contamination.
With these tips in mind, welding W1 tool steel can be accomplished successfully.
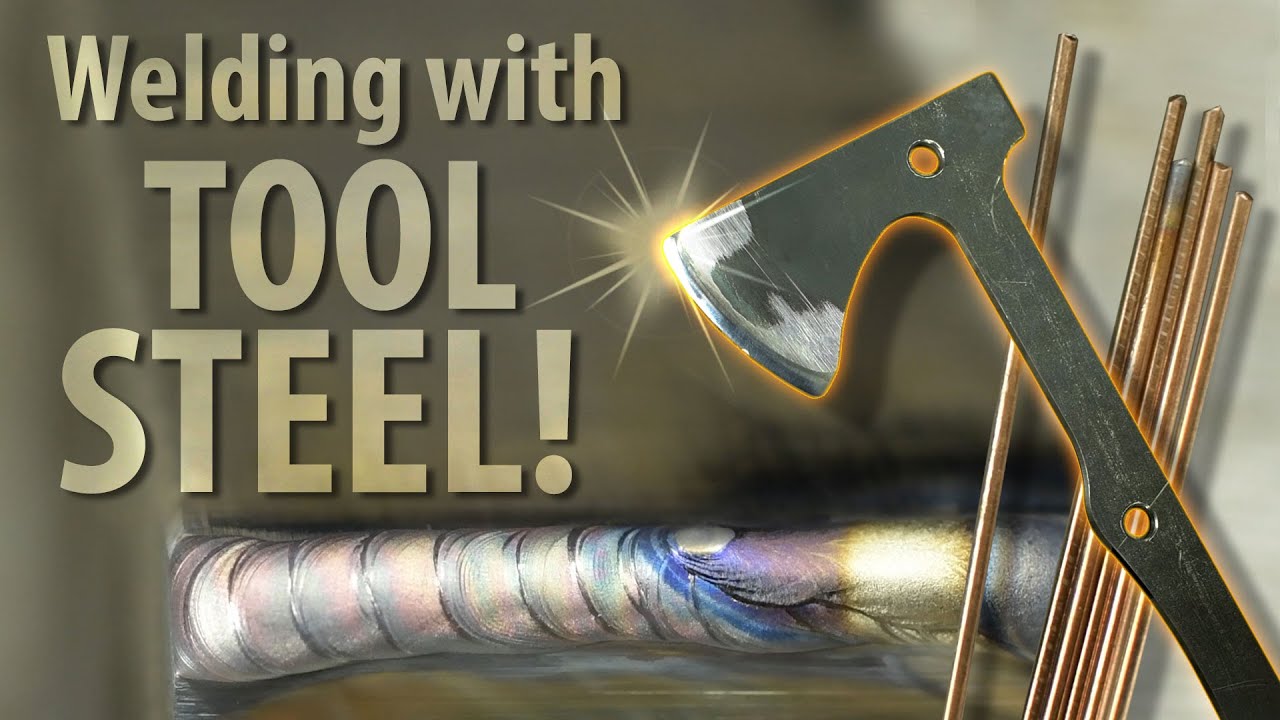
Credit: www.youtube.com
Can You Weld Steel to Mild Steel?
You can weld steel to mild steel using any welding process. The most common welding processes for joining these two metals together are oxy-fuel welding, stick welding, and MIG welding.
The key to a strong weld is to clean the surfaces of the mild steel and the steel before you start welding.
Any dirt, grease, or paint on the metal will prevent the weld from properly bonding to the metal. Once you’ve cleaned both pieces of metal, you need to choose the right filler rod for your project. For most projects, a general purpose E6010 rod will suffice.
If you’re using Oxy-fuel welding, set your welder to use an oxygen-acetylene gas mixture. This mixture provides more heat than other gas mixtures and is necessary for adequately melting both metals so they can fuse together. If you’re using Stick or MIG welding, make sure your welder is set to use low hydrogen electrodes; these types of electrodes produce less slag (a byproduct of the welding process) and are less likely to cause cracking in your welds.
Once you’ve chosen the right filler rod and set your welder properly, it’s time to start welding! Begin by tacking each piece of metal in several places so they’ll stay in place while you finish your welds. Then lay down a bead of weld along the joint between the two pieces of metal.
Make sure that each pass overlaps with the previous one so there aren’t any gaps in your final weld bead.
What Do You Weld Tool Steel With?
Welding tool steel can be tricky, as it has a high carbon content and is prone to cracking. The key is to use a low-hydrogen welding process, such as gas tungsten arc welding (GTAW) or plasma arc welding (PAW). These processes produce less heat than other methods, which helps reduce the risk of warping the steel.
If you’re working with thin sheets of tool steel, you may also be able to use resistance spot welding (RSW), which uses electrical current to create heat and join the pieces of metal together. However, RSW isn’t recommended for thicker pieces of tool steel, as it can cause the edges of the metal to distort.
Can High Strength Steel Be Welded to Mild Steel?
Yes, high strength steel can be welded to mild steel. There are a few things to keep in mind when welding these two types of steel together. First, it is important to use a low hydrogen welding process.
This will help to prevent cracking in the weld area. Second, the weld joint should be designed so that the stress is evenly distributed. This can be done by using a butt joint or lap joint configuration.
Finally, it is important to preheat the base metal before welding and to cool it slowly after welding.
Can You Weld Steel to Steel?
You can weld steel to steel using any welding process, as long as the grade of steel is compatible with the chosen welding process. For example, you can use arc welding to weld low-carbon steel to itself or to another low-carbon steel, but you cannot use arc welding to weld stainless steel to itself or another stainless steel. If you’re unsure about which welding process and filler material to use for a particular application, consult a professional welder or engineer.
TIG Welding with TOOL STEEL filler?!
Conclusion
Welding tool steel to mild steel is a process that requires two different types of welding rods, as well as a power source that is capable of handling high amperage. The first step is to weld the two pieces of metal together using a rod that is made for welding tool steel. This rod will have a higher melting point than the mild steel, which will help to prevent the tool steel from warping during the welding process.
Once the two pieces are welded together, they can then be cooled and ground down to create a smooth surface.