Welding hardened tool steel is a difficult and delicate process. The high carbon content of the steel makes it difficult to weld without causing warping or cracking. The best way to weld hardened tool steel is with an oxygen-acetylene torch.
The torch can be used to preheat the metal, which will help prevent cracking. When welding, use a short, quick strokes and maintain a low welding heat to avoid damaging the metal.
- Acquire the appropriate welding tools and materials for the job
- This includes a welder, electrode rods, wire, gas, and metal
- Clean the area to be welded thoroughly
- This ensures that there is no dirt or debris that could contaminate the weld
- Set up your welder according to the manufacturer’s instructions
- This includes connecting the gas lines and setting the power output appropriately
- Preheat the area to be welded with a torch if possible
- This helps to loosen up any impurities in the metal and makes welding easier overall
- Begin welding by holding the electrode rod close to the surface of the metal and moving it along in a fluid motion
- If you are using a wire feeder, hold the wire near the surface as well and keep it moving so that it doesn’t stick or clump up
Welding Tool Steel With 7018
Welding tool steel with 7018 is a great way to get a strong, durable weld. This type of steel is known for its strength and resistance to wear and tear. 7018 is also easy to work with, making it a good choice for welders who are new to the trade.
Here are some tips on how to get the most out of your 7018 welding rod:
-Use a low amperage when starting your weld. This will help you avoid blowing holes in your workpiece.
-Keep your arc short and sweet. Too much arc length will make your bead look flat and can lead to cracking.
-Don’t be afraid to go slow.
Take your time when welding tool steel and don’t try to rush things along.
Tool Steel Welding Electrode
When it comes to welding electrodes, there are many different types to choose from. But when you need an electrode that can weld tool steel, you need a special kind of electrode known as a Tool Steel Welding Electrode.
As the name suggests, a Tool Steel Welding Electrode is specifically designed for welding tool steel.
This type of electrode is made from a tungsten alloy and is coated with a thoriated tungsten oxide. This makes the electrode extremely durable and able to withstand high temperatures.
The biggest advantage of using a Tool Steel Welding Electrode is that it can weld tool steel at very high temperatures.
In fact, this type of electrode can weld tool steel at temperatures up to 4500 degrees Fahrenheit! That’s much higher than the melting point of most other metals.
Another advantage of using a Tool Steel Welding Electrode is that it produces very little slag.
Slag is the waste material that’s left behind after welding. It can be very difficult to remove and can cause problems if not removed properly. But because the Tool Steel Welding Electrode produces so little slag, it’s much easier to clean up afterwards.
If you need an electrode that can weld tool steel, then a Tool Steel Welding Electrode is the best choice for you. It’s able to weld at extremely high temperatures and produces very little slag.
Welding Mild Steel to Tool Steel
Welding mild steel to tool steel can be a difficult process. The two metals have different melting points, which can make it tough to create a strong bond between them. However, with the right welding techniques and materials, it is possible to weld these two metals together successfully.
Here’s what you need to know about welding mild steel to tool steel.
This type of filler metal has a high carbon content, which helps it match the carbon content of tool steel. It also has a low melting point, which makes it easier to weld without over heating the metals being joined. Once you’ve selected the right filler metal, you need to prepare your welding area properly.
Make sure that both pieces of metal are clean and free of any rust or debris. You’ll also want to use some sort of backing material behind the weld joint to help support it during the welding process. This could be something as simple as a piece of scrap wood or another piece of mild steel.
Now you’re ready to start welding! Begin by heating up both pieces of metal until they’re glowing red hot. Then, use your welder’s torch to slowly add filler metal into the joint while simultaneously moving the torch along the length of the joint.
Keep adding fillermetal until the joint is completely filled in and there’s no longer any gap between the two pieces of metal being joined together. Finally, allow everything to cool before handling or moving anything around – otherwise you risk cracking or breaking your newly welded joint!
Weld Mold 958 Alternative
Weld Mold 958 Alternative is a great way to save money and time on your welding projects. This product is an excellent weld filler that can be used in place of more expensive and time consuming alternatives. Weld Mold 958 Alternative is easy to use and provides superior results.
Welding D2 Tool Steel
Welding D2 tool steel is not for the faint of heart. This extremely hard and durable metal is used in a variety of applications that require superior wear resistance, such as cutting tools and dies. While it can be welded using traditional methods, doing so requires a great deal of skill and experience.
That being said, welding D2 tool steel can be done with relative ease if you have the right equipment and know-how. Here are a few tips to help you get started:
1. Choose the right filler metal.
When welding D2 tool steel, it’s important to choose a filler metal that has similar properties to the base metal. This will help ensure a strong bond between the two metals. 2. Use short, controlled welds.
Because D2 tool steel is so hard, it can be difficult to control your welds when working with it. To avoid this issue, use short welds that are no more than 1″ in length. 3. Keep your heat low.
Too much heat can damage the structure of D2 tool steel, making it more brittle and susceptible to breakage.
Welding M4 Tool Steel
M4 tool steel is a high-speed steel that is often used in cutting tools. It is a tungsten-molybdenum alloy with a carbon content of around 0.9%. The molybdenum gives the steel its high hardness and wear resistance, while the tungsten provides good red hardness.
The combination of these two elements makes M4 an ideal choice for cutting tools that need to retain their sharpness for long periods of time.
Steel Welding Tools
If you’re in the market for steel welding tools, you’ve come to the right place. In this blog post, we’ll provide detailed information about the different types of steel welding tools available, as well as their pros and cons.
Welding is a process that joins materials, usually metals or thermoplastics, by causing coalescence.
This is typically done by melting the workpieces and adding a filler material to form a pool of molten material (the weld pool) that cools to form a joint with properties similar to those of the base material. Welding is widely used in manufacturing and other applications where permanent joints are required.
There are several methods of welding steel, including: oxy-fuel welding, shielded metal arc welding (SMAW), gas tungsten arc welding (GTAW), flux cored arc welding (FCAW), and submerged arc welding (SAW).
Each method has its own advantages and disadvantages, which we’ll explore in more detail below.
Oxy-fuel Welding: Oxy-fuel welding (OFW) is a type of heating process that uses oxygen and fuel gases such as acetylene, propane, or natural gas. OFW is commonly used for fabrication and repairs of wrought iron gates or fences, stainless steel tubing, or brass sculptures.
Pros:
-Can be used on any type of metal
-Inexpensive equipment
-Portable
-Easy to learn
Tig Welding Rod for Hardened Steel
Tig Welding Rod for Hardened Steel
If you’re looking to weld hardened steel with a Tig welder, you’ll need to use a special type of welding rod. Hardened steel is difficult to weld because it’s so hard and brittle.
However, with the right rod, you can weld it successfully. The best type of welding rod to use for hardened steel is one made of tungsten. Tungsten is an extremely strong metal that can handle the high temperatures needed to weld hardened steel.
It’s also very resistant to wear, making it ideal for this application. When shopping for a tungsten welding rod, be sure to get one that’s specifically designed for welding hardened steel. With the right rod, you can weld hardened steel easily and effectively.
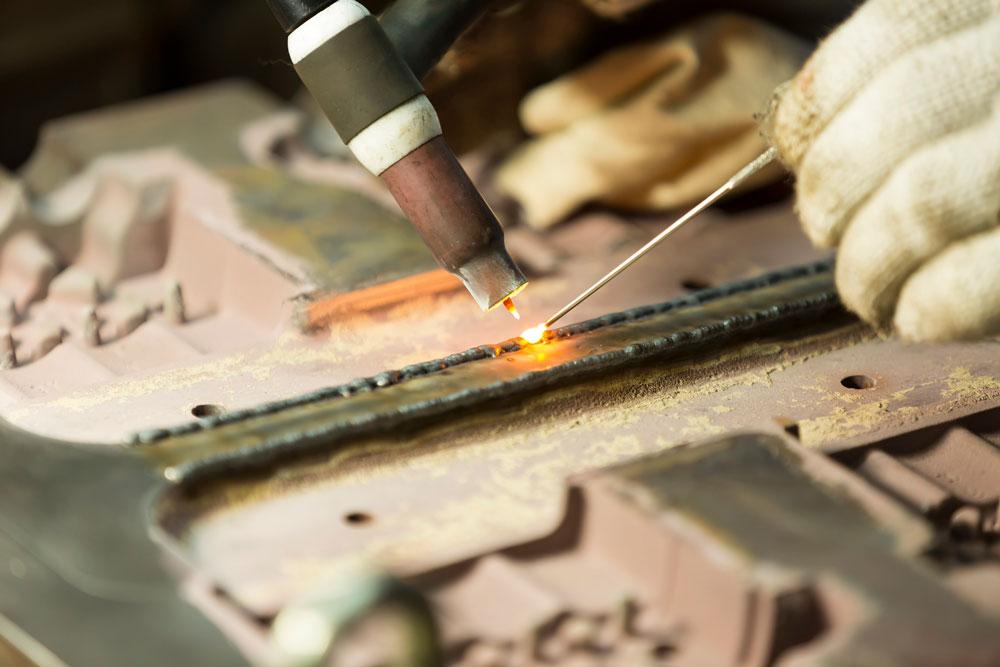
Credit: www.thefabricator.com
How Do You Weld Hardened Steel?
Hardened steel is a type of steel that has been treated with heat or cold to alter its physical and chemical properties. This makes it more resistant to wear and tear, as well as corrosion. Welding hardened steel can be tricky, as it is difficult to create a strong bond between the two pieces of metal.
The best way to weld hardened steel is by using an oxy-acetylene torch with a stainless steel welding rod. First, you will need to preheat the area you are going to weld. Then, you will need to apply the torch to the area for several seconds before adding the welding rod.
Once you have added the welding rod, continue to heat the area until the two pieces of metal have fused together.
Can You Weld on Tool Steel?
Yes, you can weld on tool steel. Tool steel is a type of carbon steel that is well-suited for making tools. It has a high carbon content and can be hardened to create a durable, hard-wearing surface.
welding on tool steel is not as difficult as some might think. In fact, with the right tools and techniques, it can be quite easy. Here are a few tips to help you get started:
1. Choose the right filler metal. When welding on tool steel, it’s important to choose a filler metal that has a low hydrogen content. This will help prevent cracking and warping of the metal during the welding process.
2. Use preheating and post-heating methods. Preheating the tool steel before welding can help prevent cracking by reducing the amount of thermal stress on the metal during welding. Post-heating after welding is also important in order to relieve any residual stresses in the metal caused by the welding process.
3 . Use appropriate cooling methods . It’s important to cool down the tool steel slowly and evenly after welding in order to prevent cracking or warping from uneven cooling rates .
One way to do this is by using watercooling methods , such as immersion cooling or circulating coolant systems .
Can I Mig Weld Hardened Steel?
Yes, you can MIG weld hardened steel. Hardened steel is steel that has been treated with heat or chemicals to make it harder than other types of steel. This means that it will be more difficult to weld than softer, untreated steel.
However, with the right equipment and techniques, it is possible to successfully weld hardened steel. Here are a few things to keep in mind when welding hardened steel:
– Use a wire feeder specifically designed for welding hard materials.
These wire feeders will have special features like higher torque and stronger drive rollers that can handle the increased resistance of the hard material.
– Use a gas mixture that is designed for welding hard materials. This gas mix will usually contain more argon and less oxygen than a standard gas mix for welding mild steel.
– Use a smaller diameter electrode when welding hard materials. This will help to minimize the amount of heat that is transferred to the material being welded, which can help prevent warping or distortion.
– Preheat the area around the joint before starting to weld.
This will help soften the metal and make it easier to weld.
Start by heating the area with an oxy-acetylene torch until it is red hot, then let it cool until it is just barely warm before beginning to weld.
What Techniques are Recommended for Welding Tool Steels?
Different types of tool steels have different compositions and therefore require different welding techniques. For example, high-carbon tool steels are difficult to weld because they are prone to cracking. Low-carbon tool steels are less likely to crack, but they may be more difficult to weld because they can form martensite (a hard, brittle microstructure) during cooling.
One recommended technique for welding high-carbon tool steels is called preheating. This involves heating the steel before welding to help prevent cracking. Another recommended technique is called post-weld heat treatment (PWHT).
This involves heating the steel after welding in order to relieve stress and prevent warping or distortion.
For low-carbon tool steels, it is often recommended to use a filler metal that contains chromium. This will help prevent the formation of martensite during cooling.
It is also important to avoid overheating the steel while welding, as this can also lead to martensite formation.
TIG Welding with TOOL STEEL filler?!
Conclusion
If you’re looking to weld hardened tool steel, there are a few things you need to keep in mind. First, you need to use a filler material that has a higher melting point than the base metal. Second, you need to preheat the metal before welding.
And finally, you need to post-weld heat treat the metal to ensure it is properly hardened. With these tips in mind, welding hardened tool steel is a relatively simple process.