A2 tool steel is a high carbon alloy that is often used for making cutting tools and other wear-resistant parts. It can be difficult to weld, but with the proper equipment and techniques, it is possible to create strong welds. Here are some tips on how to weld A2 tool steel.
- Cut the A2 tool steel to the desired shape and size
- Clean the surface of the A2 tool steel with a wire brush or grinding wheel
- Set up your welding equipment according to the manufacturer’s instructions
- Strike an arc on the A2 tool steel and begin welding
- Weld slowly and evenly, making sure to keep the weld pool small
- Finish welding and allow the piece to cool before removing it from the welding table
Welding M4 Tool Steel
M4 tool steel is a high speed steel that is often used in applications where wear resistance and toughness are required. It has excellent hot hardness and can be heat treated to produce a wide variety of properties. This article will discuss the welding of M4 tool steel, including the best methods and techniques to use.
How to Weld Tool Steel
When it comes to welding tool steel, there are a few things that you need to keep in mind. Tool steel is a bit different than other types of steel, and as such, requires a different approach when welding. Here are a few tips on how to weld tool steel:
1. Use the right type of electrode. When welding tool steel, you want to use an electrode that is specifically designed for this purpose. There are two main types of electrodes that can be used for welding tool steel – hardfacing electrodes and covered electrodes.
Hardfacing electrodes have a higher carbon content, which makes them ideal for weldingtool steel. Covered electrodes, on the other hand, have a lower carbon content and are better suited for general purpose welding.
2. Preheat the metal before welding.
This is especially important when working with thicker pieces of tool steel. By preheating the metal, you can help prevent cracking and warping during the welding process.
3. Use slower speeds when welding.
Because tool steel is harder than other types of Steel , you will need to use slower speeds when Welding . This will help prevent the electrode from becoming too hot and melting through the metal . 4 .
Cool down gradually after Welding Once you’ve completed your welds , it’s important to let the metal cool down gradually . If you cool it down too quickly , it could crack or warp .
Tool Steel Welding Electrode
Tool steel is a type of carbon steel that is well-suited for making tools. It has a high carbon content and is often used to make knives, drill bits, and other cutting tools. Tool steel welding electrodes are specially designed to weld tool steel.
They have a higher carbon content than standard welding electrodes, which makes them ideal for welding tool steel.
Welding Tool Steel With 7018
If you’re a welder, then you know that 7018 is one of the most popular welding rods. But what do you really know about it? Here’s a quick guide to help you better understand this versatile and widely used welding rod.
7018 is a low-hydrogen electrode that produces smooth, stable arcs with minimal spatter. It works well on a variety of metals, including mild steel, high-strength steels, and cast iron. It can be used for both AC and DC welding, making it a versatile choice for many welders.
One of the main advantages of 7018 electrodes is that they produce strong welds with good impact resistance. This makes them ideal for use in applications where the weld will be subject to stress or vibration. They also have good tolerance to cold cracking, which makes them ideal for use in colder climates.
7018 electrodes are available in two different types: fast-fill and standard-fill. Fast-fill electrodes have higher deposition rates than standard-fill electrodes, so they’re often used when speed is important. However, they can be more difficult to control and may cause porosity problems if not used correctly.
Standard-fill electrodes are easier to use and provide more consistent results, making them the better choice for most welders. Whether you’re an experienced welder or just starting out, 7018 welding rod is a great choice for many projects. With its versatility and dependability, it’s sure to become one of your go-to welding supplies.
Welding Mild Steel to Tool Steel
Welding mild steel to tool steel is a process that can be performed using various welding methods, including oxy-acetylene welding, arc welding, and resistance welding. Each method has its own advantages and disadvantages, so it’s important to choose the right method for the job at hand.
Oxy-acetylene welding is a popular choice for welding mild steel to tool steel because it’s relatively easy to do and doesn’t require any special equipment.
However, it’s not recommended for large projects or for projects where precision is essential.
Arc welding is another option that can be used to weld mild steel to tool steel. It’s more difficult than oxy-acetylene welding but produces a higher quality weld.
This method is also better suited for larger projects or projects where precision is key.
Resistance welding is the third option available for welding mild steel to tool steel. It uses electrical current to create heat, which then melts the metals being joined together.
This method is best suited for small projects or projects where speed is more important than accuracy.
A2 Tool Steel Tig Rod
If you’re in the market for a high-quality tig rod, then you should definitely consider A2 tool steel. This type of steel is often used in applications where strength and durability are key, such as in the aerospace industry. It’s also a popular choice for knife making and other similar projects.
A2 tool steel is composed of carbon, manganese, chromium, molybdenum, and vanadium. It’s known for being tough and resistant to wear and tear. It can be heat treated to increase its hardness, but it’s not recommended to weld this type of steel without first consulting with a professional.
If you’re looking for a tig rod that will give you superior results, then A2 tool steel is definitely worth considering. Keep in mind that this type of steel is best suited for specific applications, so make sure it’s the right choice for your project before making your purchase.
Welding D2 Tool Steel
Welding D2 Tool Steel is a high carbon, high chromium tool steel that is known for its excellent abrasion and wear resistance properties. It is often used in applications where wear and tear are a concern, such as in cutting tools and dies. D2 tool steel can be welded using all standard welding methods, but care must be taken to avoid overheating the steel during welding.
Welding W1 Tool Steel
Welding W1 tool steel is a process that can be used to join two pieces of this type of metal together. This is done by using heat to melt the metals at their edges and then cooling them so that they form a bond. This type of welding is considered to be very strong and is often used for joining together metal parts that will be under high levels of stress or strain.
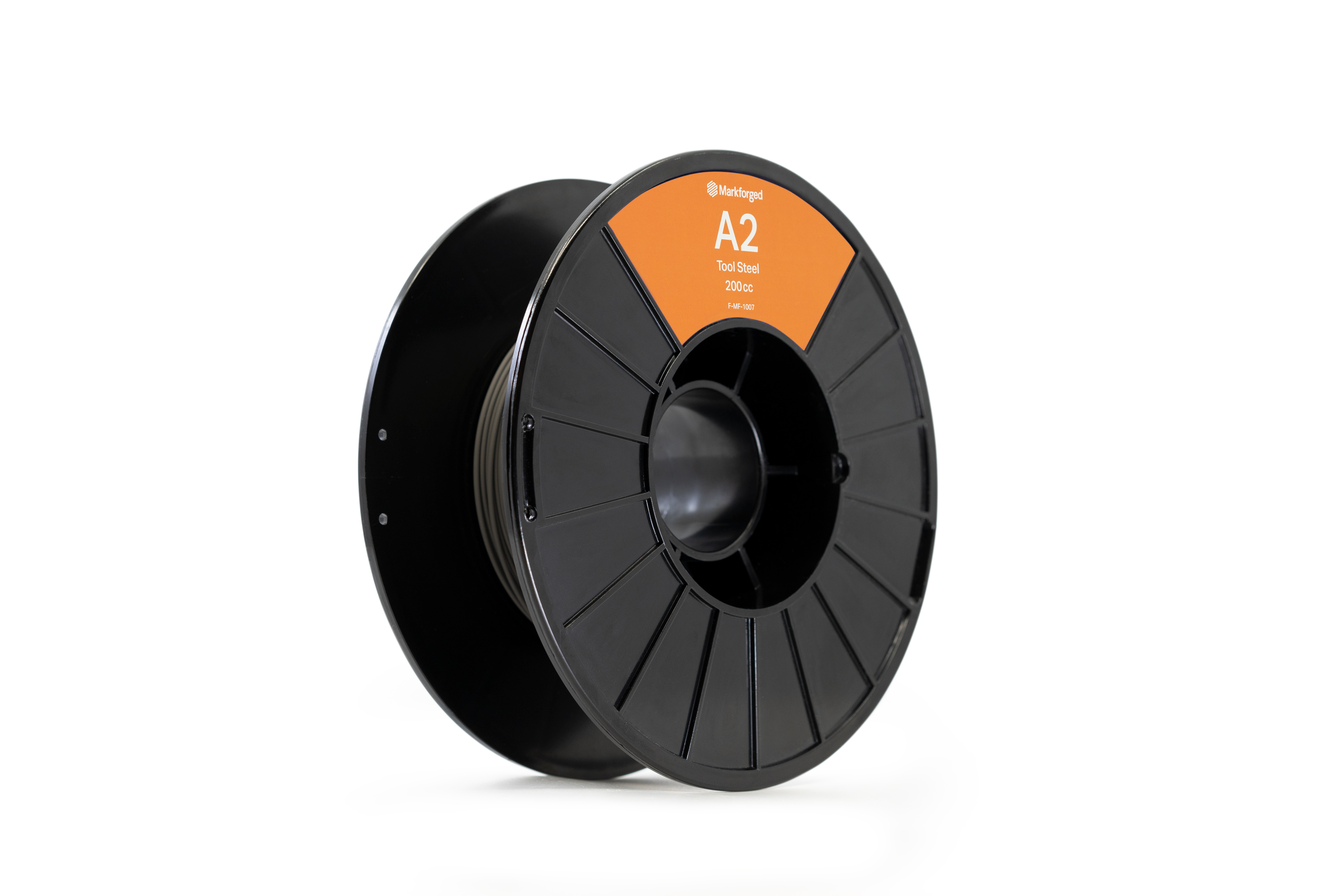
Credit: www.designfusion.build
Can A2 Be Welded?
Yes, A2 can be welded. However, it is not generally recommended because of the high carbon content. When welding A2, preheat is essential to avoid cracking, and the use of low hydrogen electrodes is recommended.
Can Tool Steel Be Welded?
Yes, tool steel can be welded. However, it is important to note that there are different grades of tool steel, and each grade will have different welding properties. For example, some grades of tool steel are designed to be resistant to high temperatures, while others are more corrosion-resistant.
Therefore, it is important to consult the manufacturer’s instructions or a professional welder before attempting to weld tool steel.
What Techniques are Recommended for Welding Tool Steels?
There are several factors to consider when welding tool steels, such as the type of steel, the application it will be used for, and the desired properties of the weld. The most common types of tool steels are carbon steels, alloy steels, and high-speed steels. Each type of steel has its own set of characteristics that need to be taken into account when selecting a welding technique.
The three most common welding processes for tool steel are gas metal arc welding (GMAW), plasma arc welding (PAW), and oxy-fuel gas welding (OFW). GMAW is the most versatile of the three processes and can be used with all types of tool steel. It is also the fastest process and produces welds with good strength and ductility.
PAW is best suited for high-speed steels due to its ability to produce extremely hard welds. OFW is typically used for carbon steels because it produces welds with high impact toughness.
For example, if high hardness is needed then PAW or GMAW using hardfacing filler metals would be appropriate. If higher impact toughness is needed then OFW or GMAW using low hydrogen electrodes would be better choices. Ultimately, the best way to select a welding technique for tool steel is to consult with an experienced welder or metallurgist who can help you choose the right process and filler metal for your specific application.
How Do You Weld D2 Tool Steel?
D2 tool steel is a high carbon and high chromium alloy that has been heat treated to achieve extremely high hardness levels. It is often used in applications where wear resistance is required, such as in knives, dies and cutting tools. welding D2 tool steel can be a challenge due to its high carbon content and hardening properties.
Here are some tips to help you successfully weld this tough material:
1. Use a low current setting – Welding D2 tool steel at too high of a current can cause the metal to overheat and crack. Start with a lower current setting and increase it until you find the sweet spot that works for your particular setup.
2. Use short, quick welds – Another way to prevent overheating is by using shorter, quicker welds instead of long, drawn-out ones. This will help keep the overall heat input down while still providing a strong weld joint.
3. Preheat the metal – If possible, preheating the metal before welding will help reduce the risk of cracking during cooling afterwards.
You can do this by simply placing the D2 piece on an oven safe surface and heating it up to around 400 degrees Fahrenheit for 20-30 minutes prior to welding.
4. Use proper shielding gas – When welding D2 tool steel, it’s important to use an appropriate shielding gas mix in order to prevent oxidation of the weld joint area. A common mix used for this purpose is 90% helium/10% argon but other variations may be recommended depending on your specific application needs.
TIG Welding with TOOL STEEL filler?!
Conclusion
Tool steel is a type of carbon steel that is well-suited for making tools. It has a high carbon content and can be hardened to create a durable, hard-wearing surface. A2 tool steel is one variety of tool steel that is particularly well-suited for use in making tools.
In this blog post, we will show you how to weld A2 tool steel so that you can create strong, reliable welds that will hold up under heavy use.
Welding A2 tool steel can be done using any welding process, but the most common are arc welding and oxyacetylene welding. For best results, it is important to use a low hydrogen electrode and preheat the metal before welding.
When welding A2 tool steel, it is also important to cool the metal slowly to prevent cracking.