If you’re rebuilding a differential or swapping out gears, you’ll need to set the pinion bearing preload. This is usually done with a torque wrench, but if you don’t have one handy, there’s an alternative method. First, find a nut that fits snugly on the end of the pinion shaft.
Thread it onto the shaft and tighten it until it bottomed out. Then, using a small pry bar or screwdriver, lever against the side of the nut to rotate the pinion shaft. As you rotate the shaft, keep an eye on the backlash between the ring gear and pinion teeth.
- Remove the nut and washer from the end of the shaft
- Insert a feeler gauge between the end of the shaft and the bearing surface
- Tighten the nut until there is a slight drag on the feeler gauge
- Hold the nut in place and remove the feeler gauge
- Install a new locknut and torque to specifications
Too Much Pinion Preload Symptoms
If your pinion preload is too high, you may notice some symptoms while driving. The first symptom is usually a vibration coming from the rear of the vehicle. This can be caused by the driveshaft being out of balance or by the U-joints being worn.
If you continue to drive with this condition, you may eventually hear a loud noise coming from the rear end as well. This noise is typically caused by the gears grinding against each other. In extreme cases, the pinion nut can come loose and cause damage to the gear teeth.
If this happens, it will need to be replaced.
Another symptom of too much pinion preload is increased fuel consumption. This is because the engine has to work harder to turn the wheels when there is excessive preload on the pinion gear.
You may also notice that your vehicle doesn’t accelerate as quickly as it did before. This is due to increased friction between the gears which reduces efficiency.
Ultimately, if you suspect that your pinion preload is too high, it’s best to have it checked out by a professional mechanic who can make any necessary adjustments.
How is Pinion Bearing Preload Checked And Adjusted
Pinion bearing preload is the force required to rotate the pinion shaft when the vehicle is at rest. The amount of preload determines how much friction is present between the bearings and the shaft, and affects how long the bearings will last.
To check pinion bearing preload, a torque wrench is used to measure the amount of force required to turn the pinion shaft.
The proper amount of preload can be determined by consulting a service manual for your specific vehicle make and model.
Once you know the proper amount of preload for your vehicle, you can adjust it accordingly. To adjust pinion bearing preload, special tools are required which can be rented or purchased from most auto parts stores.
With these tools in hand, follow these steps:
1) Remove the differential cover and drain any fluid that may be inside.
2) Loosen the adjusting nut until there is no longer any resistance when turning the pinion shaft.
Do not remove this nut completely.
3) Turn the adjusting screw in small increments until you reach the desired amount of preload according to your service manual. Each full turn of this screw should equal approximately 2-3 ft lbs of torque added to achieve desired effect (check with your service manual to determine an exact number).
4) Once desired level of preload has been reached, back out adjusting screw slightly (approximately 1/8th – 1/4th turn), then retighten locking nut against it until snug (do not overtighten).
How to Check Pinion Bearing Preload
If you’re a do-it-yourselfer, checking pinion bearing preload is something you can do at home with a few tools. Here’s how:
1. Jack up the vehicle and support it securely on jack stands.2. Remove the rear wheels. 3. Using a pry bar or large screwdriver, remove the fill plug from the differential housing. This will allow you to check the fluid level.
The fluid should be at the bottom of the fill hole when properly filled. Add or remove fluid as necessary to achieve this level. 4. With the fill plug removed, locate the adjusting nut on the end of the pinion shaft .
This is usually located near where one of the axle shafts enters the differential housing .
Pinion Bearing Preload Tool
If you’re a gearhead, then you know that preload is critical to maintaining proper function of your pinion bearings. Too much preload and you risk damaging the bearings; too little preload and they’ll wear out prematurely. That’s why having a good quality pinion bearing preload tool is essential.
There are a few different ways to measure pinion bearing preload, but the most common is with a dial indicator. This type of tool attaches to the yoke or carrier and measures the amount of axial movement in the bearings as they rotate.
Another way to measure preload is with a feeler gauge.
This method is less precise but can be used if you don’t have access to a dial indicator. Simply insert the feeler gauge between the races of the bearings and see how much resistance there is to movement.
Once you know how much preload is necessary, it’s time to adjust it.
This is done by adding or removing shims from between the bearing caps and adjusting nuts. It’s important to do this slowly and carefully so that you don’t over- or under-tighten the nut, which could damage the threads or cause other problems.
With a little patience and attention to detail, setting your pinion bearing preload correctly will extend the life of your bearings and help keep your drivetrain running smoothly for years to come!
Symptoms of Over Tighten Pinion Nut
If you’ve ever had a car with a rear-wheel drive, you know that there’s a pinion nut that helps to keep the drive shaft in place. But what happens when this nut gets over tightened?
There are a few symptoms that will let you know if your pinion nut is over tightened, and it’s important to pay attention to these so you can avoid any serious damage to your car.
One symptom is unusual noise coming from the rear of the car. This can be anything from a grinding sound to a metallic clunking. It’s important to listen for this because it’s one of the first signs that something is wrong back there.
Another symptom is vibration in the steering wheel or seat. This is caused by the drive shaft being out of alignment and trying to find its way back into place. The vibration will usually get worse the faster you’re going, so it’s definitely something you’ll notice while driving.
If you feel this, it’s important to get your car checked out as soon as possible.
The last symptom is leaking fluid from the rear end of the car. This could be anything from oil to transmission fluid, and it’s usually an indication that there’s something seriously wrong back there.
If you see any kind of leak, it’s important to take your car in for service right away.
These are just some of the symptoms of an over tightened pinion nut – if you notice any of them, don’t hesitate to take your car in for service so a mechanic can take a look and fix the problem before it causes any more damage!
Pinion Preload Noise
If you have ever heard a loud clicking noise coming from your car, it may be due to pinion preload noise. This is caused by the differential gear not being properly lubricated, and can be quite annoying. Luckily, there are a few things you can do to fix the problem.
First, check the level of your differential fluid. If it is low, top it off and see if that helps solve the problem. If not, you may need to replace the fluid altogether.
You can also try adding a thicker grade of fluid, as this may help reduce the noise. If neither of these solutions work, it is likely that your differential gears need to be replaced. This is a more serious issue and will require professional help.
However, if you catch it early enough, replacing the gears should fix the problem and eliminate the pinion preload noise for good!
What Can Happen If the Pinion Bearing Preload was Set Incorrectly?
If the pinion bearing preload is set incorrectly, a number of problems can occur. The most common problem is that the bearings will fail prematurely. This can lead to expensive repairs and downtime for your vehicle.
Other problems that can occur include:
-The gears may not mesh correctly, leading to noise and vibration.
-The axleshaft may become misaligned, causing increased wear on the tires and suspension components.
-The differential may not work properly, resulting in reduced traction and performance.
It is important to have the pinion bearing preload set correctly to avoid these potential problems. If you are unsure how to do this, consult a professional mechanic or technician.
Pinion Bearing Preload Torque Wrench
Pinion Bearing Preload Torque Wrench
A pinion bearing preload torque wrench is a specialized tool that is used to apply the correct amount of torque to a pinion nut, in order to achieve the correct preload on the bearings. This type of wrench is typically used in conjunction with a dial indicator, in order to ensure that the desired amount of torque is achieved.
There are two main types of pinion bearing preload torque wrenches: hydraulic and pneumatic. Hydraulic wrenches use oil pressure to generate the required torque, while pneumatic wrenches use air pressure. Both types of wrenches can be adjusted to deliver the precise amount of torque needed for a particular application.
When using a pinion bearing preload torque wrench, it is important to follow the manufacturer’s instructions carefully in order to avoid damaging the bearings or other components. In general, it is best to err on the side of too much rather than too little torque, as excessive preload can cause damage, but insufficient preload will lead to premature bearing failure.
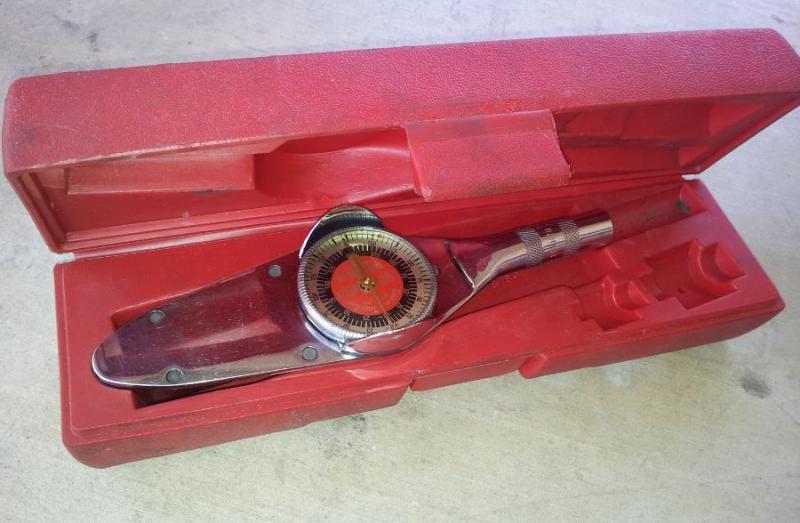
Credit: www.peachparts.com
How Do You Set Pinion Bearing Preload?
When it comes to setting pinion bearing preload, there are a few different methods that can be used. The most common method is to use a hydraulic press. This method is quick and easy, and doesn’t require any disassembly of the differential.
Simply place the differential in the press, apply pressure to the yoke until the desired preload is achieved, and then tighten down the bolts.
Another common method is to use shims. This method is a bit more involved, as it requires disassembling the differential and removing the carrier bearings.
Once the carrier bearings are removed, shims of varying thicknesses can be used to achieve the desired preload on the pinion bearings. This method does require some trial and error to get right, but once you’ve done it a few times it’s not too difficult.
The last method is to use threaded adjusters.
This method is similar to using shims, except that instead of shims you’re using threaded adjusters that screw into place. This allows for much finer adjustments to be made, which can be helpful if you’re having trouble getting things just right with shims. However, like with shims, this method does require some trial and error before you get it dialed in correctly.
Whichever method you choose, setting pinion bearing preload is an important step in properly assembling your differential. Do some research and experiment with different methods until you find one that works best for you.
What Tool Do You Use to Check Pinion Bearing Preload?
If you’re working on a car, truck, or SUV with a conventional differential (as opposed to a locking differential or limited-slip differential), then you’ll need to check the preload on the pinion bearings. This is a simple process that can be done with just a few tools.
First, you’ll need a torque wrench.
Second, you’ll need a dial indicator. You can find both of these at any auto parts store.
To check the preload, first remove the fill plug from the differential cover.
Then slowly turn the torque wrench clockwise until it stops. The reading on the dial indicator should be between 12 and 15 inch-pounds. If it’s outside of that range, then you’ll need to adjust the bearing preload accordingly.
What Happens If Pinion Preload was Set Incorrectly?
If pinion preload is set incorrectly, it can cause a number of problems. Most notably, it can lead to excessive wear on the bearings and/or gear teeth, and can also cause unusual noises. Additionally, incorrect pinion preload can result in premature failure of the bearings or gear teeth.
How Tight Should a Pinion Nut Be?
There are a few different schools of thought on how tight a pinion nut should be, and ultimately it comes down to personal preference. Some mechanics will swear by torquing the nut to spec, while others will simply tighten it until the play in the yoke is eliminated. There isn’t necessarily a right or wrong answer, but we’ll run through the pros and cons of each method so you can decide what works best for you.
Torquing to spec is obviously the more accurate method, and if done properly will result in a properly tightened pinion nut every time. The downside is that it can be time consuming, and if you’re not careful you can easily strip the threads on the nut. If you go this route, make sure to use a quality torque wrench that is calibrated regularly.
The “hand tight” method is definitely quicker and easier, but doesn’t always result in the ideal pinion nut tightness. It’s important to note that even though you may eliminate all play in the yoke with this method, you could still be well under or over the recommended torque specs. This isn’t necessarily a bad thing as long as you check your work frequently and make adjustments as needed, but it’s something to be aware of.
Easily set pinion preload torque with a floor jack
Conclusion
If you’re rebuilding your differential, or even just replacing your pinion bearings, you’ll need to set the preload. This is usually done with a torque wrench, but if you don’t have one handy, there’s an easy way to do it without one.
First, install the new bearings and races on the pinion shaft.
Next, install the yoke and tighten the nut until it’s snug. Now, with a pry bar or similar tool, rotate the yoke until you feel resistance. At this point, there should be about 10-15 inch-pounds of preload on the bearings.
If you don’t have a torque wrench, this is a good time to stop and check your work.
If everything feels good, continue rotating the yoke another quarter turn or so. This will give you a little extra insurance against bearing failure down the road.
And that’s all there is to it! With a little patience and attention to detail, you can easily set pinion bearing preload without a torque wrench.