If your air compressor pump is not working as it should, don’t despair. With a little time and effort, you can rebuild your air compressor pump and have it working like new again.
- If your air compressor pump is not working properly, you may need to rebuild it
- To rebuild your air compressor pump, you will need a few tools and supplies, including: a wrench set, a socket set, an air compressor rebuild kit specific to your model of air compressor, and some lubricating oil
- First, use the wrench set to remove the four bolts that hold the pump head in place on the cylinder body
- Once the bolts are removed, lift off the pump head
- Next, use the socket set to remove the piston from the cylinder sleeve
- Inspect the piston and cylinder for any damage or wear and replace as necessary
- Clean all parts with compressed air or solvent and then dry thoroughly before reassembling
- Lubricate all moving parts with oil before reassembly
- Reassemble the piston into the cylinder sleeve and then replace the pump head onto the cylinder body using the four bolts removed earlier
- Torque down evenly using a cross pattern until snug
- 8 Double check all connections are secure before operating
Air Compressor Pump Rebuild Kit
An air compressor is a device that increases the pressure of air by compressing it. A pump rebuild kit helps to keep your air compressor in good working condition by rebuilding the pump when it starts to wear out.
1.5 Hp Air Compressor Pump
An air compressor is a device that increases the pressure of air by compressing it. A 1.5 horsepower air compressor pump is a common type of air compressor, typically used to power tools such as nail guns.
The 1.5 hp air compressor pump works by drawing in atmospheric air and compressing it using a piston.
The compressed air is then delivered through an outlet valve at a much higher pressure than the surrounding atmosphere.
The main advantage of using an air compressor is that it can store large amounts of energy in the form of compressed air, which can bereleased quickly and easily when needed. This makes them ideal for powering tools that require high levels or sudden bursts of power, such as impact wrenches and pneumatic hammers.
There are many different types and sizes of air compressors available on the market, so it’s important to choose one that’s suitable for your needs. If you’re only going to be using it occasionally, then a portable model might be sufficient. However, if you need a more powerful machine for industrial applications, then a stationary unit would be better suited.
How to Identify Air Compressor Pump
An air compressor pump is a vital component of any air compressor, and it is important to know how to identify one when you are shopping for a new or replacement unit. There are several different types of air compressor pumps on the market, and each has its own unique set of features and benefits. Here is a quick guide to help you choose the right air compressor pump for your needs:
Piston Air Compressor Pumps: These pumps are typically used in small, portable air compressors. They work by using a piston to draw in air and then compress it inside the cylinder. Piston pumps are typically very durable and reliable, but they can be noisy and may require more maintenance than other types of pumps.
Rotary Air Compressor Pumps: These pumps use two rotating vanes to draw in air and compress it inside the chamber. Rotary pumps are usually quieter than piston pumps and require less maintenance, but they may not be as durable.
Centrifugal Air Compressor Pumps: These pumps use an impeller to draw in air and then spin it at high speeds to compress it inside the housing.
Centrifugal pumps are typically very efficient and can reach high pressures, but they may not be as durable as other types of pumps.
Twin Cylinder Air Compressor Pump Rebuild Kit
If you have a twin cylinder air compressor pump, then at some point you will need to rebuild it. This is not a difficult task, but there are a few things you need to know before you start.
The first thing you need to do is gather all the necessary parts.
You can find most of these at your local hardware store or online. The main thing you need is a new piston and rings, as well as gaskets and seals. You may also need new connecting rods and bearings, depending on the condition of your existing ones.
Once you have all the parts, the next step is to disassemble your pump. This is relatively straightforward – just follow the instructions in your manual. Be careful with the gaskets and seals, as they can be easily damaged.
Now it’s time to start rebuilding your pump. First install the new piston and rings, making sure everything is properly seated and aligned. Next install the connecting rods and bearings, again making sure everything fits snugly into place.
Finally, put on all the new gaskets and seals.
Once everything is installed, simply reassemble your pump following the directions in your manual. Once complete, your pump should be as good as new!
Air Compressor Pump Repair near Me
If your air compressor suddenly stops working, it may be due to a problem with the pump. If you’re looking for air compressor pump repair near me, there are a few places you can check out.
The first place to look is your local hardware store.
They may have a service center that can take a look at your pump and make the necessary repairs.
Another option is to contact the manufacturer of your air compressor. They may have authorized service centers that can help you with your pump problem.
Finally, you can check online for companies that specialize in air compressor pump repair. There are many reputable companies out there that can provide you with the help you need to get your pump up and running again.
Rebuild Air Compressor Car
If your car has an air compressor, chances are it’s going to need to be rebuilt at some point. Here’s a detailed look at what goes into rebuilding an air compressor car.
The first step is to remove the old compressor from the car.
This will involve removing any brackets or other attachments that are holding it in place. Once the old compressor is out, you’ll need to clean up the area where it was mounted. This will help ensure a good seal when you install the new compressor.
Next, you’ll need to select a new air compressor. Be sure to choose one that is compatible with your car model and make. You’ll also want to make sure it has enough power to meet your needs.
Once you have your new compressor, follow the instructions that come with it for installation.
After your new air compressor is installed, be sure to test it out before taking your car on the road. This will help ensure that everything is working correctly and that there are no leaks.
Assembly And Disassembly of Air Compressor
An air compressor is a machine that uses an electric motor or gasoline engine to power a device that pulls air into a chamber and compresses it. The compressed air is then used to power other tools or machines. Air compressors are found in a variety of settings, including industrial plants, automotive shops, and even some home garages.
While there are many different types and sizes of air compressors, they all operate on the same basic principle. Compressed air is created by drawing air into a chamber and then rapidly increasing the pressure inside that chamber. This increase in pressure forces the air to occupy less space, which results in the compression of the air.
Once the desired level of compression has been reached, the compressed air is then released from the chamber through an outlet valve. The outlet valve can be connected to another tool or machine that will use the compressed air, or it can simply be released into the atmosphere. The assembly and disassembly of an air compressor is not a difficult task, but there are several important steps that must be followed in order to ensure proper function and safety.
When assembling an air compressor, always begin by reading the manufacturer’s instructions carefully. It is also important to make sure that all parts are clean and free of debris before starting assembly. Once all of the necessary parts have been gathered, assembly can begin by attaching the intake hose to the compressor body.
Next,the electric motor or gas engine should be mounted onto the compressor body according to manufacturer’s instructions . Once these two main components have been properly installed ,the unit can be filled with oil if necessary . Finally ,the output hose should be attached to direct compressed air where it will be needed .
At this point ,your compressor should be fully assembled and ready for use . When it comes time to disassemble your compressor for cleaning or storage ,the process is fairly simple . Begin by disconnecting any hoses or other attachments from the unit .
Next ,remove any bolts or screws holding down the motor or engine . With these major components removed ,you should now have access to most of the inner workings of your compressor . Be sure to consult your owner’s manual for specific instructions on how to safely clean each component .
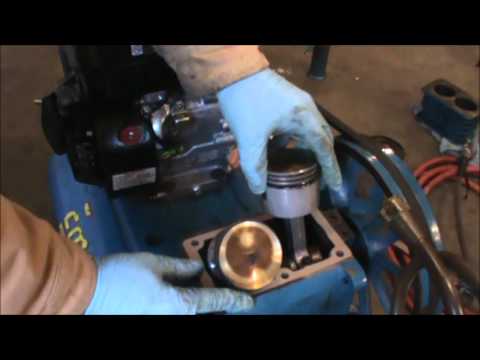
Credit: www.youtube.com
Can Air Compressor Pumps Be Rebuilt?
An air compressor pump is a mechanical device that converts power into potential energy by compressing air. Air compressors are used in a variety of applications, from powering tools in a garage to inflating tires on a car. Many air compressor pumps can be rebuilt, although the process may vary depending on the make and model of the pump.
Before beginning a rebuild, it is important to consult the owner’s manual for your particular air compressor pump. This will provide valuable information about the parts and their locations, as well as any special tools that may be required for the job. Once you have gathered the necessary materials, follow these steps to rebuild your air compressor pump:
1) Disassemble the pump according to the instructions in your owner’s manual. Be sure to keep track of all small parts and fasteners as you work.
2) Inspect all of the components for wear or damage.
If any parts are damaged beyond repair, they will need to be replaced before proceeding with the rebuild.
3) Clean all of the parts using compressed air or an ultrasonic cleaner. This will remove any dirt or debris that could cause problems during reassembly.
4) Lubricate all moving parts with fresh oil before reassembling them according to the instructions in your owner’s manual. Pay close attention to any areas that may require special lubrication, such as O-rings or bearings.
5) Reattach any external fittings or hoses before starting up your air compressor pump for the first time after the rebuild.
Make sure all connections are secure before operating the unit.
How Do You Fix an Air Compressor That Won’T Build Pressure?
If you have an air compressor that won’t build pressure, there are a few things you can do to try and fix the problem. First, check the intake filter to see if it is clogged. If it is, replace it with a new one.
Next, check the unloader valve to see if it is stuck open. If so, clean or replace it as needed. Finally, check the pressure switch to see if it is faulty.
If so, replace it with a new one.
What are 3 Common Issues Problems With a Pneumatic Air Compressor?
Compressors are one of the most important pieces of equipment in many industries. They are used to power a variety of tools and machines, and they can be found in factories, workshops, and construction sites around the world. Despite their widespread use, compressors can sometimes experience problems that can impact their performance.
Here are three common issues that can occur with pneumatic air compressors:
1. Leaks
One of the most common problems that can occur with a pneumatic air compressor is a leak.
Compressors rely on seals to keep air from escaping, but these seals can sometimes wear out or become damaged. This can cause air to leak out of the compressor, which will reduce its efficiency and cause it to work harder than necessary. If you notice anyLeaks coming from your compressor, it’s important to have them repaired as soon as possible.
2. Overheating
Another issue that can occur with pneumatic air compressors is overheating. The motor that powers the compressor creates a lot of heat, and if this heat isn’t dissipated properly, it can damage the compressor.
Overheating can also lead to premature wear on components such as bearings and belts. To prevent overheating, make sure your compressor is installed in a well-ventilated area and that there is plenty of airflow around it when it’s running. You should also regularly check the coolant level in the compressor’s cooling system (if applicable) and add more if necessary.
3 . Vibration
Excessive vibration is another problem that can affect pneumatic air compressors (and other types of machinery).
Vibration can cause damage to components and make noise pollution levels unacceptable in some cases. It can also lead to fatigue for operators who have to work with vibrating machinery for extended periods of time. To solve this problem, make sure your compressor is properly mounted on a solid foundation using vibration-damping materials (e..g., rubber pads).
How Do You Service an Air Compressor Pump?
If you’re like most people, you probably don’t think about your air compressor pump until it stops working. But if you want to keep your air compressor in top shape, it’s important to service it regularly. Here’s how to do it:
1. Start by draining the oil from the pump. You can do this by removing the drain plug and letting the oil drain into a catch pan. Once the oil has drained, replace the drain plug and fill the pump with fresh oil.
2. Next, check the air filter and clean or replace it if necessary. A dirty air filter can cause all sorts of problems, so it’s important to keep it clean.
3. Now take a look at the belts that drive the pump.
If they’re worn or frayed, they need to be replaced. Belts are relatively inexpensive and easy to replace, so there’s no excuse for not doing it when they need it.
4. Finally, check all of the bolts that hold everything together on the pump.
Make sure they’re tight and free of rust or corrosion. If any of them are loose or damaged, replace them before using the pump again.
By following these simple steps, you can ensure that your air compressor pump is always in good working condition!
Burned out Air Compressor tear down, what went wrong?
Conclusion
If your air compressor pump is broken, don’t despair! You can rebuild it with a few simple tools and some elbow grease. First, remove the pump from the compressor unit.
Next, disassemble the pump by removing the connecting rods, cylinder head, valves, and piston rings. Once everything is disassembled, clean all of the parts thoroughly. Then, reassemble the pump using new gaskets and seals.
Finally, reinstall the pump on the compressor unit and you’re good to go!